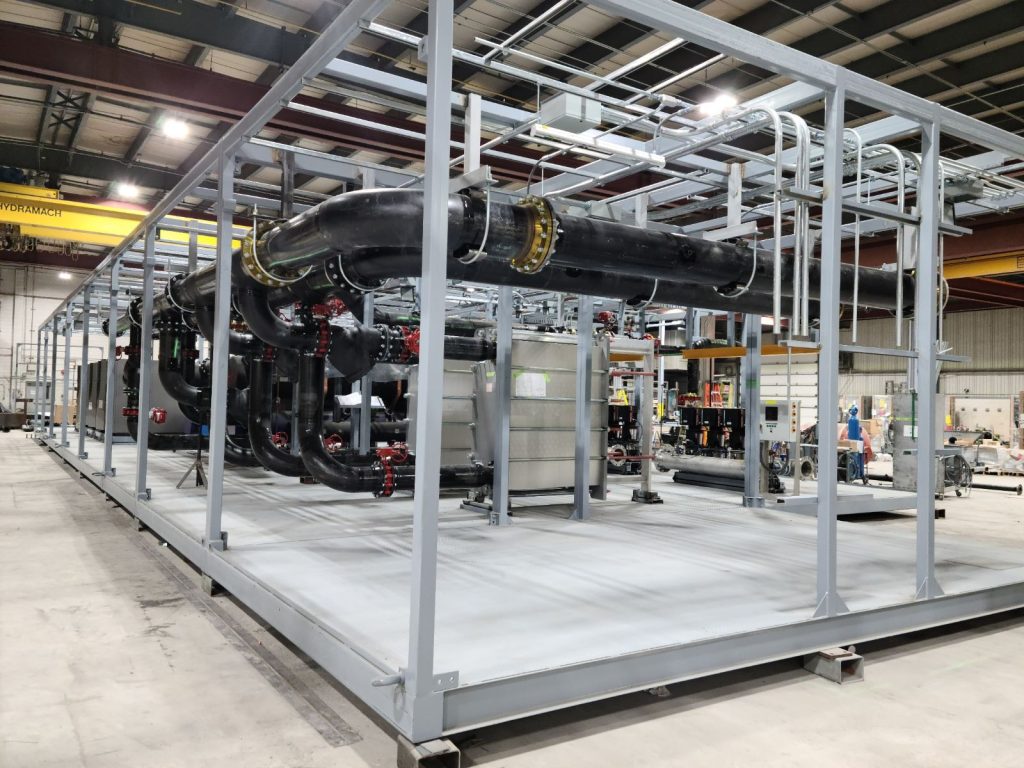
Nei prossimi anni il preassemblaggio off-site dei componenti impiantistici potrebbe diventare uno dei principali fattori di sviluppo del settore delle costruzioni, grazie alle opportunità che esso offre per realizzare edifici di alta qualità riducendo costi, tempi e impatto ambientale.
Il metodo della prefabbricazione di componenti impiantistici viene utilizzato già da anni in ambito industriale con l’assemblaggio off-site di gruppi di pompaggio, centrali termiche e piping, come pure nel settore navale con l’impiego di cellule bagno prefabbricate. In ambito civile finora il maggior numero di progetti è stato realizzato nei paesi del Golfo e nel Regno Unito, in particolare nella City di Londra dove è ormai prassi comune realizzare edifici con intere sezioni di impianti che arrivano in cantiere già premontate su skid in modo da essere installate direttamente in poche ore (figura 1).
La strategia di fornire in cantiere componenti preassemblati in fabbrica è nota con il termine Design For Manufacture and Assembly (DFMA) ed è stata senza dubbio favorita dalla disponibilità di strumenti digitali di costo accessibile per la modellazione e la progettazione in 3D (figura 2), nonché dall’integrazione fino alla dimensione 7D offerta dal metodo BIM.
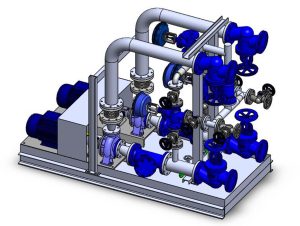
srl)
La diffusione di questa tecnica di costruzione ha permesso di apprezzare una serie di significativi vantaggi che includono la riduzione dei costi e dei tempi di costruzione, la creazione di ambienti di lavoro più sicuri, il mantenimento di una forza lavoro stabile e la riduzione (o l’eliminazione) della necessità di varianti in corso d’opera. Ciò spiega il motivo per cui sta diventando sempre più comune costruire in fabbrica componenti e sottosistemi impiantistici, sia su misura sia prodotti in serie, per poi assemblarli in cantiere collegandoli alle reti di distribuzione dei diversi impianti.
Riducendo al minimo le opere di installazione in loco è possibile costruire edifici e impianti non solo in modo più rapido, sicuro ed economico, ma anche più efficienti in termini di utilizzo delle risorse. In definitiva, se ben gestito, un progetto basato sulla prefabbricazione è quindi in grado di garantire i requisiti di tipo ambientale, sociale e aziendale alla base del concetto ESG (Environmental, Social, Governance) che rappresenta l’obiettivo degli operatori del settore delle costruzioni che sono orientati alla sostenibilità.
Maggiore produttività
Nel contesto attuale di carenza di manodopera qualificata, risulta fondamentale adottare soluzioni in grado di rendere il lavoro di installazione più facile ed efficiente. Il potenziale di crescita del settore delle costruzioni è stato finora frenato dalla scarsa produttività, significativamente inferiore a quella del settore manifatturiero che ha invece visto un aumento del 50% della produzione per ora lavorata tra il 1994 e il 2015.
In un documento pubblicato da Bryden Woods nel 2017, che analizza gli scenari per la creazione di un mercato per gli edifici prefabbricati, si evidenzia come la scarsa produttività e la carenza di manodopera qualificata causano fino al 37% dei ritardi nei cantieri. Tra le numerose e diverse misure proposte per aumentare l’efficienza, la fabbricazione off-site presenta un notevole potenziale effetto positivo se si considera che i risultati di una ricerca hanno dimostrato come la produttività del personale in fabbrica sia dell’80% rispetto al 20% di quella in cantiere.
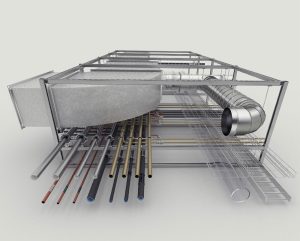
preassemblati
Un approccio DfMA riduce le ore di lavoro in loco e aumenta la produttività in quanto in fabbrica viene impiegato personale esperto che opera in impianti di produzione all’interno di ambienti coperti protetti dalle intemperie, dove si riducono al minimo i problemi associati all’umidità, ai rischi atmosferici e alla sporcizia. Inoltre, i componenti vengono assemblati lavorando a terra invece che a un’altezza che in alcuni cantieri può superare i 4 metri. Ciò aumenta in modo sostanziale i livelli di produttività, oltre che di sicurezza.
Un tipico esempio è costituito da elementi modulari realizzati con telai in acciaio (figura 3) ai quali sono fissati tubi e canali per approntare dorsali orizzontali e montanti verticali preassemblati da sollevare e posizionare in cantiere (figura 4). La riduzione del numero di lavoratori presenti in cantiere riduce la necessità di spostamenti o di sistemazioni temporanee in loco, con i relativi impatti ambientali ed economici.
In definitiva la prefabbricazione può essere considerata, in primis, come uno strumento per ottenere un risparmio sui costi e quindi maggiori profitti per gli operatori.
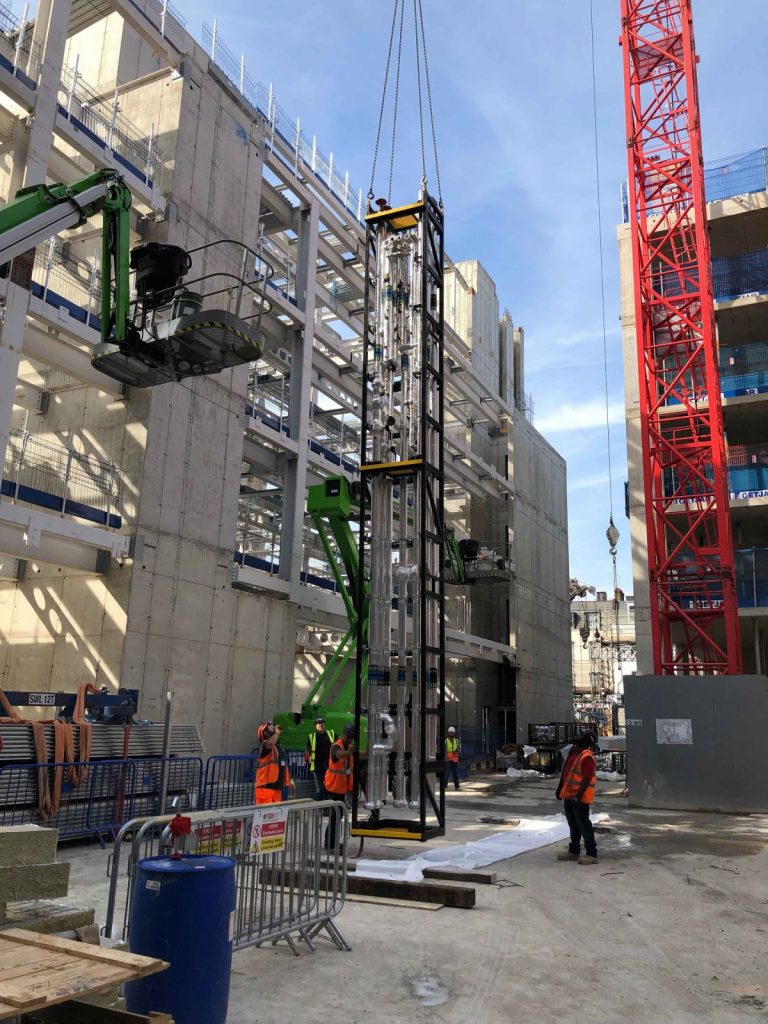
Qualità dei componenti e impatto ambientale
La costruzione dei componenti in fabbrica fornisce impianti di qualità superiore in quanto consente di effettuare un più efficace monitoraggio del lavoro eseguito e di ridurre al minimo gli errori di montaggio (figura 5). Inoltre, utilizzando un ambiente di produzione controllato basato su standard appropriati, i componenti di un impianto possono essere costruiti con una qualità uniforme per soddisfare le esigenze del committente rispettando al tempo stesso i requisiti legislativi e normativi.
Con la produzione in fabbrica si riduce anche la necessità di prendere decisioni in loco, e quindi il rischio di ritardi, ed è possibile sviluppare soluzioni standardizzate che incoraggiano attività più approfondite di prova e verifica.
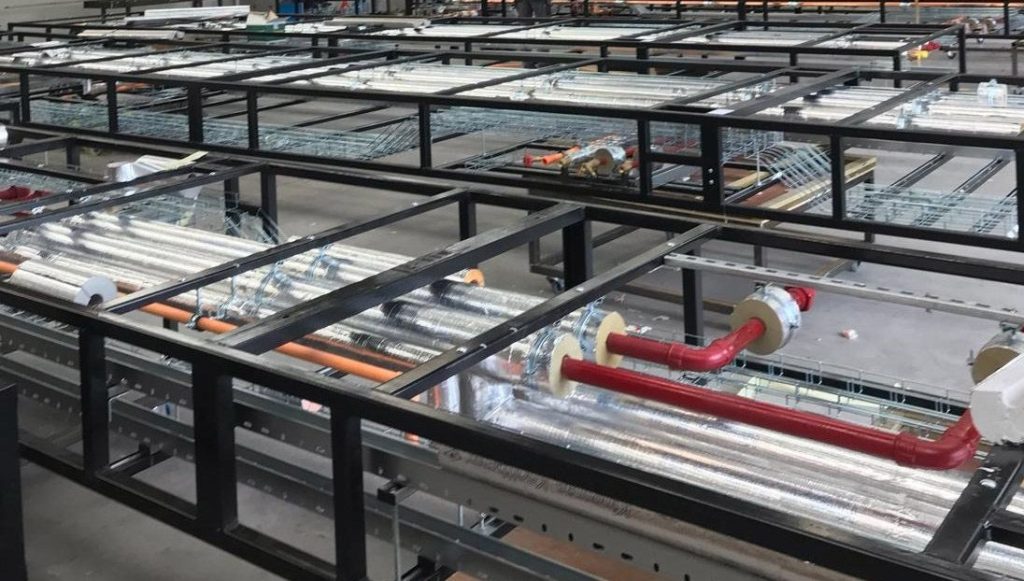
La prefabbricazione può trarre vantaggio dalle tecniche di produzione sempre più sofisticate in grado di garantire anche una sensibile riduzione degli sprechi di materiale. Grazie al metodo DfMA è possibile ridurre del 70-90% la quantità di rifiuti prodotta dal cantiere e fino al 20% l’inquinamento su base locale grazie al minore numero di lavorazioni eseguite e alla riduzione del traffico di veicoli in prossimità del sito.
Grazie alle operazioni di assemblaggio e commissioning eseguite in officina si ottiene anche un miglioramento delle prestazioni degli impianti che può portare a una riduzione fino al 30% delle emissioni equivalenti di anidride carbonica. Infine, si riduce anche l’impatto del cantiere per quanto riguarda il rumore prodotto.
Tracciamento e ciclo di vita
I componenti assemblati in fabbrica possono essere facilmente tracciati mediante etichette e tag RFID oppure con QR code attraverso tutto il processo, dalle fasi di produzione e assemblaggio fino a quelle di impiego, manutenzione ed eventuale sostituzione e smaltimento. Combinati con tecnologie come BIM e blockchain, questi metodi di codifica e tracciamento sono in grado, potenzialmente, di fornire registrazioni permanenti per scopi di audit gestionale e di feedback degli utenti.
Ciò consente di disporre di dati in fase di utilizzo, di conseguenza i costi e l’impatto del ciclo di vita possono essere misurati in modo più adeguato e, idealmente, aumentano le opportunità per realizzare un’effettiva economia circolare.
Sicurezza e aspetti sociali
Se adeguatamente gestiti, gli ambienti di costruzione in fabbrica presentano anche minori rischi per la sicurezza, la salute e il benessere del personale, con le relative responsabilità per il datore di lavoro. Le apparecchiature possono essere assemblate in reparti di produzione completamente accessibili, che utilizzano apparecchiature di sollevamento, utensili di lavoro e misure di sicurezza appositamente concepiti e che beneficiano di un’adeguata illuminazione, ventilazione e controllo del rumore.
Limitando il numero di ore in cantiere si ottiene una riduzione dell’80% degli incidenti (figura 6).
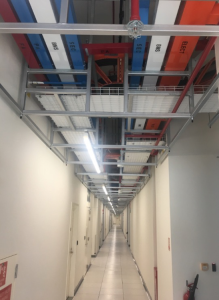
Nel documento pubblicato dall’Health and Safety Executive (HSE) del Regno Unito sulla produzione off-site, si sottolinea anche l’importanza delle opportunità offerte in termini di creazione di occupazione in aree lontane dal cantiere. Ciò può essere particolarmente vantaggioso in caso di carenza di competenze a livello locale e può ampliare le opportunità per la formazione a lungo termine di lavoratori qualificati, oltre a ridurre la necessità degli spostamenti (con i relativi impatti ambientali ed economici).
In caso di progetti di grande taglia che richiedono la prefabbricazione di numerosi sottosistemi, può essere conveniente realizzare una struttura di produzione nei pressi del cantiere, in grado anche di promuovere l’impiego di manodopera locale.
Innovazione e standardizzazione
Un approccio basato sulla prefabbricazione può stimolare le opportunità di sviluppare progetti innovativi in termini di razionalizzazione della progettazione, ottimizzazione nella scelta e nell’uso dei materiali, consegne just-in-time o pianificazione logistica al fine di raggiungere elevati tassi di produttività in loco. L’obiettivo è quello di fornire un progetto che soddisfi le esigenze dell’utente riducendo al minimo costi, tempi ed emissioni inquinanti, ottimizzando gli effetti positivi in termini di salute, sicurezza e qualità.
Il metodo DfMA può essere applicato sia a progetti di edifici piccola e taglia scala, sia a progetti di grandi dimensioni. I componenti progettati con strumenti digitali possono essere utilizzati su progetti diversi, riducendo così al minimo la necessità di riprogettare ogni volta sistemi su misura. Ciò significa, ad esempio, che un singolo componente potrebbe essere utilizzato come parte dell’impianto a servizio di una scuola, di un ospedale o di un palazzo uffici.
Il concetto di “personalizzazione di massa” si basa su una tecnica di produzione che combina la flessibilità dei prodotti sviluppati su misura con i bassi costi unitari associati alla produzione in serie. Grazie ai progressi nei metodi di produzione digitale, come la robotica e la stampa 3D, in futuro sarà possibile realizzare questa strategia a costi ancora inferiori.
Ogni singolo sottosistema prefabbricato può essere progettato utilizzando strumenti BIM e metodi di progettazione assistita dal computer (CAD) in 3D, consentendo ai diversi soggetti interessati di collaborare allo sviluppo del sistema e di valutarne la funzionalità prima dell’inizio dei lavori, riducendo il rischio di ritardi nel cronoprogramma.
Centrali preassemblate
Sono numerosi gli esempi in cui la strategia DfMA può essere utilizzata per realizzare centrali preassemblate. La figura 7 mostra un esempio di applicazione dello strumento di modellazione 3D per ottimizzare la prefabbricazione relativa alla sostituzione di una centrale termica a servizio di un edificio per il terziario, che ha consentito di minimizzare il tempo di fermo impianto, obiettivo primario dato che gli uffici dovevano rimanere operativi.
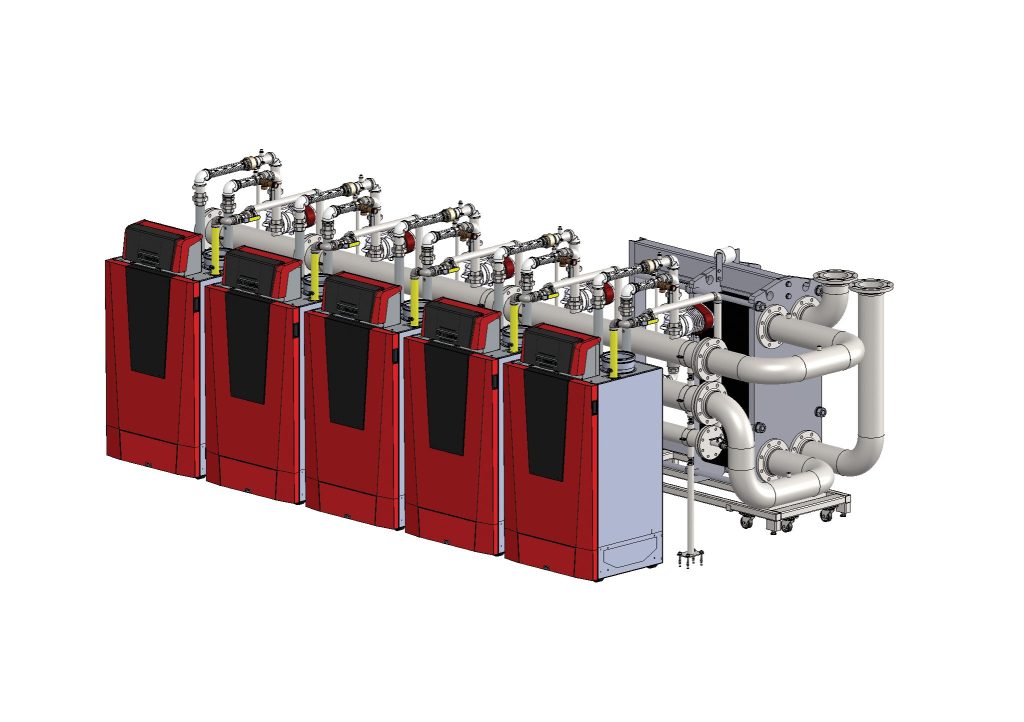
Il produttore ha collaborato con l’appaltatore nel progettare una disposizione personalizzata dei componenti integrando caldaie, tubazioni e scambiatore di calore a piastre in un sistema modulare prefabbricato, riducendo i tempi e la manodopera in cantiere e ottimizzando l’uso dello spazio disponibile.
Dal canto suo, l’appaltatore ha predisposto le tubazioni di collegamento prima della consegna dei moduli, che sono stati trasportati in loco, collegati e messi in funzione, rimettendo in funzione il sistema di riscaldamento in brevissimo tempo e rispettando così la data di consegna dell’intervento.
Applicando un approccio di montaggio su skid, in cui i componenti sono installati su una struttura in acciaio che può essere sollevata e facilmente installata sul posto, è possibile consegnare al sito un sistema progettato e ingegnerizzato con precisione che soddisfa le esigenze e i requisiti della struttura dell’edificio, presentando inoltre dimensioni tali da garantire un’agevole movimentazione dell’elemento prefabbricato attraverso le vie di accesso disponibili.
Lo skid integra gli stessi componenti che altrimenti verrebbero installati separatamente in un tradizionale processo di installazione in situ, come caldaie, ventilatori, pompe (complete di accumuli inerziali), valvole, tubazioni, controlli e sensori. Lo skid viene progettato appositamente per garantire che possa essere trasportato senza danneggiare i componenti, posizionato con precisione sul posto e ce possa anche compensare eventuali imprecisioni nelle opere civili, come ad esempio le irregolarità dei solai.
I moduli più piccoli possono essere uniti tra loro per fornire sistemi più grandi già sottoposti a commissioning, riducendo così il tempo necessario sul posto per mettere in funzione gli impianti. La figura 8 mostra un booster per l’acqua calda sanitaria montato su skid progettato su misura per un’applicazione specifica che prevedeva un programma di cantiere molto breve.
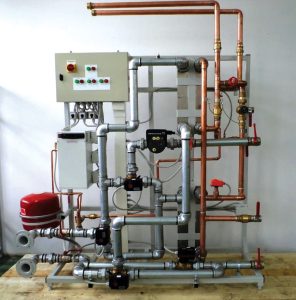
L’utilizzo di questa soluzione prefabbricata e completamente testata ha garantito che i tempi di realizzazione in sito fossero ridotti al minimo.
Le tecniche DfMA possono essere impiegate per realizzare moduli su misura, come il sistema mostrato nelle figure 9 e 10: una centrale termica autonoma e preassemblata, interamente realizzata all’interno di un container ISO, progettata per soddisfare i requisiti di riscaldamento di un edificio plurifamiliare. La centrale è stata completamente costruita, testata e collaudata in fabbrica, per essere poi consegnata in cantiere e sollevata con una gru come un monoblocco (figura 11).
Infine, l’installatore ha effettuato i collegamenti all’impianto termico prima del completamento del commissioning finale e della messa in servizio dell’impianto.
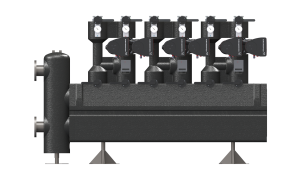
L’impiego di componenti preassemblati rappresenta una soluzione conveniente anche negli interventi di sostituzione di singoli componenti delle centrali termiche, dove risulta fondamentale ridurre al minimo il fermo impianto, specialmente nei casi di produzione sanitaria centralizzata. A tale scopo sono disponibili sistemi modulari standardizzati (figura 12) che comprendono separatori idraulici, collettori di distribuzione e gruppi di rilancio (diretti o miscelati), già completi di isolamento termico, prese di pressione, pozzetti porta-sonda ed intercettazioni.
Sistemi di facciata
Una soluzione molto innovativa per gli edifici per uffici è costituita dall’integrazione di terminali ad induzione direttamente nelle facciate continue. Il terminale viene installato in fabbrica nel modulo di facciata e in cantiere deve essere soltanto collegato alle reti di distribuzione dell’aria e dell’acqua. Ciò significa che all’interno dell’ambiente non è necessario prevedere uno spazio per l’installazione dei terminali a pavimento, a parete o a soffitto.
L’unica parte visibile è il diffusore lineare per la mandata dell’aria situato nella parte superiore della facciata. Il terminale ad induzione può essere dotato di batteria a 2 o a 4 tubi e garantisce raffreddamento, riscaldamento e ventilazione. Può essere fornito di sistema di controllo anch’esso già montato in fabbrica. Il servomotore della valvola di regolazione e la sonda di temperatura sono forniti con un cavo pronto per essere collegato al sistema bus e alla linea in bassa tensione.
L’integrazione nel modulo di facciata garantisce, oltre alla riduzione dei tempi di esecuzione, un’elevata flessibilità di progettazione degli spazi e rappresenta una soluzione ottimale per interventi di ristrutturazione di edifici esistenti con una ridotta altezza utile di interpiano.
Un nuovo metodo di lavoro
Fondamentale per il successo dell’approccio DfMA è l’adozione di processi di progettazione e costruzione in grado di garantire un approccio integrato e coordinato basato sulla collaborazione lungo l’intera catena del valore, che coinvolga quindi committente, progettista, installatore e produttori off-site. Un progetto sviluppato pensando al DfMA già durante la fase di concept pone le basi per garantire l’efficienza del processo nelle successive fasi esecutive e costruttive.
Per un progettista di impianti finora il termine “progettazione integrata” ha significato collaborare fianco a fianco con gli altri specialisti (architetti, strutturisti) allo scopo di sviluppare un progetto coordinato. Nell’ambito del metodo DfMA il concetto deve evolversi in modo da abbracciare tre elementi: progettazione, fabbricazione e installazione.
Ciò richiede un profondo cambiamento della mentalità che i diversi attori in gioco devono adottare. Infatti, mentre in campo industriale la fabbricazione da sempre è intimamente integrata all’attività di progettazione per la produzione e l’assemblaggio dei componenti in serie, altrettanto non si può dire per il settore delle costruzioni.
Finora i progettisti hanno operato in modo isolato con l’obiettivo di creare quello che, in base alla propria esperienza personale, ritengono essere il progetto più efficiente ed economico per soddisfare le esigenze del committente. Dal canto loro, le imprese di installazione sono sempre alla ricerca di soluzioni per realizzare le opere al minor costo, spesso a scapito della qualità del progetto. Mettere intorno allo stesso tavolo progettisti, installatori e produttori di componenti rappresenta un obiettivo non semplice da raggiungere. Il modo in cui il settore delle costruzioni sarà in grado di evolversi in questa direzione rappresenta il fattore fondamentale per l’effettiva applicazione del metodo DfMA.
Collaborazione e coordinamento
La prefabbricazione off-site richiede quindi che ingegneri, architetti, imprese e tutte le figure con un ruolo critico del team di progetto lavorino insieme in modo efficiente. Il concetto di progettare, fabbricare e installare assemblaggi completi mediante la collaborazione tra le diverse discipline può consentire una maggiore precisione e quindi impianti più organizzati, puliti ed efficienti, rispetto alle strategie tradizionali che richiedono settimane per essere progettate e che possono comportare confusione, disorganizzazione e inefficienza. Gli elementi costitutivi dei cantieri di oggi sono concepiti per soddisfare requisiti di legge e di funzionalità utilizzando gli stessi metodi impiegati negli ultimi 100 anni.
Quando si progetta con una visione proiettata al futuro, i progettisti devono adottare un approccio diverso basato sulla collaborazione con l’impresa installatrice. Definire gli obiettivi della progettazione risulta fondamentale nella fabbricazione off-site. Quando un installatore deve costruire i componenti come sistemi preassemblati, i progettisti devono utilizzare nuovi metodi che riducano al minimo l’impiego di manodopera in loco. Soltanto così la strategia di prefabbricazione favorisce un ciclo di costruzione efficiente.
La chiave per il successo di un progetto basato sulla prefabbricazione è che tutte le parti coinvolte partecipino alla fase di concept design prima di sviluppare il modello di costruzione off-site. Ciò elimina la necessità di modifiche al progetto. Rispetto alle strategie di costruzione tradizionali, la prefabbricazione deve essere eseguita in modo più efficiente anche perché per definizione il processo deve essere coordinato affinché pos sa funzionare. Di conseguenza, è necessario un livello più elevato di controllo di qualità per prefabbricare off-site e poi trasportare i sistemi preassemblati in cantiere.
Gli strumenti di progettazione
Utilizzare questo metodo di lavoro coordinato e trovare partner sul lato della costruzione che abbiano capacità e volontà di farlo rappresenta un cambiamento di paradigma. Forme contrattuali come il Design/Build cercano di riunire i membri del team secondo un obiettivo finanziario comune. Sebbene queste pratiche siano utili, il vero principio guida deve essere il fatto che i membri del team responsabili della progettazione e della costruzione desiderino lo stesso risultato e puntino verso lo stesso obiettivo (figura 13).
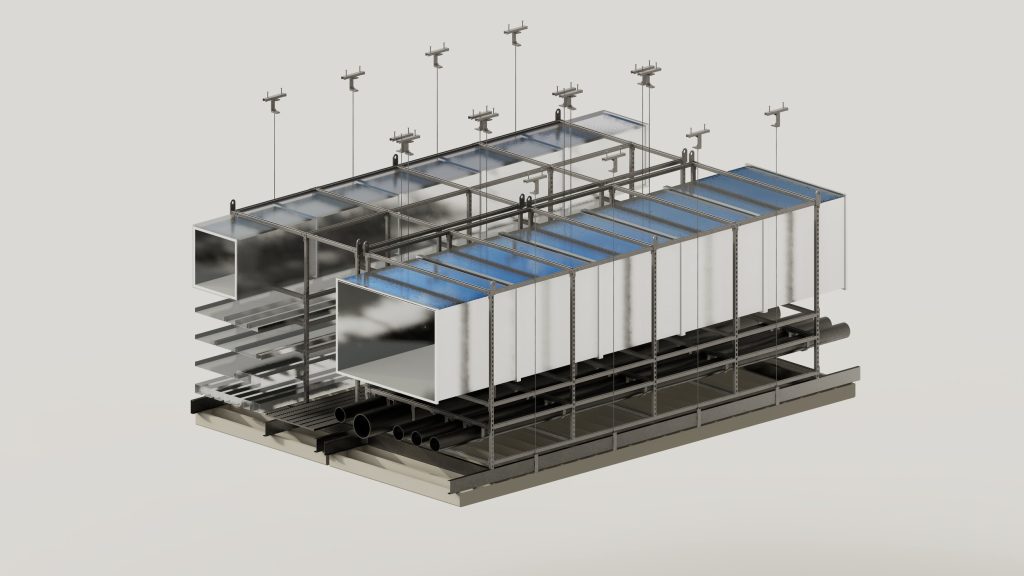
Il software di progettazione collaborativa utilizza input forniti da un calcolo di base del carico di uno spazio e lo trasforma in un modello energetico basato su informazioni limitate all’uso dell’edificio. Questi stessi strumenti tengono conto dei componenti assemblati in fabbrica che costituiranno il sistema.
Ad esempio, per quanto riguarda i canali in lamiera, nel modello le condotte non rappresentano soltanto un vincolo spaziale, ma anche dettagli costruttivi come classe di pressione, spessore e tipo di lamiera, modalità costruttive delle giunzioni longitudinali e trasversali.
Questi strumenti forniscono le conoscenze necessarie per un obiettivo produttivo in contemporanea alla progettazione iniziale. Inoltre, consentono lo sviluppo di assemblaggi integrati in cui le reti idriche, aerauliche, antincendio ed elettriche sono tutte realizzate in un unico ambiente off-site e sono installati in poche ore, anziché in giorni con avviene con i metodi tradizionali. A prescindere da strumenti, tecnologie e innovazioni disponibili, tutti i membri del team devono essere sulla stessa lunghezza d’onda per garantire il buon esito del progetto.
Sebbene la prefabbricazione sia utilizzata soprattutto nei progetti di nuova costruzione, essa può applicarsi anche agli interventi di ristrutturazione e alla sostituzione delle apparecchiature esistenti, considerando i vincoli e i requisiti specifici di ciascun progetto. Ad esempio, un locale tecnico che necessita di una nuova apparecchiatura potrebbe avere una serie di doppie porte attraverso le quali far passare il sistema preassemblato che, a tale scopo, potrebbe essere dotato di pannelli rimovibili.
Le sfide da superare
I progettisti devono affrontare numerose sfide con la prefabbricazione. La prima consiste nel mantenere una mentalità collaborativa. Se il progettista non lavora con questo approccio, l’appaltatore deve riprogettare il lavoro oppure ciò limiterà l’efficienza del team nell’ambito del progetto. È fondamentale che il progettista collabori con il partner responsabile della fase di costruzione con la stessa mentalità nei confronti della prefabbricazione utilizzando una metodologia di costruzione snella.
I progettisti non dovrebbero sentirsi minacciati nel consentire a qualcun altro di progettare elementi chiave di un impianto, come ad esempio una centrale frigorifera modulare. Essi restano sempre responsabili della progettazione e rimangono coinvolti nel processo dato che il loro dovere deontologico resta quello di fare gli interessi del committente, che solitamente la costruzione off-site garantisce sotto diversi aspetti, ad esempio in termini di costi, tempistica, sicurezza e qualità.
Un’altra sfida è quella di lavorare a fianco delle altre discipline. Nelle fabbriche o nelle officine risulta fondamentale la capacità di riunire tutte le attività e di coordinarle per essere efficienti. Per questo motivo la pianificazione, il processo e il flusso di lavoro richiedono la comunicazione tra le diverse squadre di specialisti quali tubisti, canalisti, elettricisti e altro ancora. Lavorare insieme agli altri operatori significa anche trattarli con il massimo rispetto. Questa può essere una sfida perché può accadere che i diversi subfornitori siano contrattualizzati dalle diverse parti interessate, ad esempio alcuni dal committente tramite l’architetto e altri dall’appaltatore generale. Ciò può influenzare il comportamento dei vari attori coinvolti.
Il settore HVAC non si è ancora evoluto fino al punto in cui la prefabbricazione rappresenta un metodo standard di costruzione. Lavorare all’interno di questa evoluzione in atto può essere impegnativo, poiché i diversi operatori si trovano in fasi diverse del processo di apprendimento e di adozione.
Il costo rappresenta un’altra barriera da superare. Per una piccola azienda, gli strumenti e le strutture utilizzate per la prefabbricazione sono ancora costosi. Una volta che le aziende avranno implementato il processo, l’investimento verrà ripagato, ma per gli appaltatori e le società di ingegneria più piccole, il costo può continuare a rappresentare un ostacolo.
Lessons learned
Dalle esperienze già maturate è possibile trarre lezioni importanti. L’applicazione del DfMA non è sempre l’opzione più economica e il costo dipende dalle caratteristiche specifiche del progetto. Nel valutare l’opportunità di successo della prefabbricazione off-site è necessario considerare una serie di fattori:
- la “qualità tecnica” dell’installazione (che può includere più parametri) dei sistemi fabbricati in fabbrica;
- la ripetibilità, che aumenta l’efficacia della produzione del sottosistema;
- una comunicazione efficace tra il team di cantiere e la fabbrica;
- una logistica adeguatamente pianificata ed eseguita, in assenza della quale il DfMA probabilmente è destinato a fallire, indipendentemente dalla “qualità” tecnica del sistema prefabbricato.
Affinché il settore delle costruzioni possa davvero abbracciare un approccio “industriale” i costruttori dovranno investire in nuove linee di produzione, tecnologie e risorse, e questa innovazione dovrà essere sostenuta da incentivi pubblici.
Il filo conduttore delle diverse opzioni di prefabbricazione è rappresentato dal fatto che esse richiedono a tutti i soggetti coinvolti nel processo di pensare in termini di progettazione per la produzione e l’assemblaggio fin dalla fase iniziale, come parte del generale programma di digitalizzazione e innovazione nel settore delle costruzioni.
Un’industria in evoluzione
Indipendentemente dalle barriere e dalle sfide legate ai costi, l’industria si sta muovendo in questa direzione e scegliere di non adottare questa strategia ora potrebbe avere un impatto negativo in futuro. Poiché i concetti dell’Industria 4.0 come i gemelli digitali, la fabbricazione off-site e il BIM sono sempre più utilizzati, essi si possono integrare tra loro.
Il BIM rappresenta infatti un prerequisito di base per la costruzione modulare e i gemelli digitali utilizzano il modello BIM. Se le imprese più piccole non hanno la capacità di investire in un impianto di produzione su larga scala, esse possono comunque adottare la mentalità della prefabbricazione, analizzando con spirito critico i processi e le tecniche di costruzione esistenti e trovando il modo di renderli più snelli o di coordinarli con le altre discipline. Ad esempio, le tubazioni in PVC utilizzate negli impianti sanitari possono essere tagliate a misura prima di essere inviate al cantiere in quanto ciò consente di ridurre i tempi di installazione. I piccoli appaltatori possono utilizzare questo metodo e preparare i componenti in officina in modo che in cantiere devono soltanto assemblarli come i pezzi di un Lego.
Un altro esempio è l’assemblaggio in fabbrica delle schermature dei WC già complete di tubazioni di scarico e di ventilazione che in cantiere possono essere rapidamente sollevate e posizionate riducendo il tempo di installazione da ore a minuti. Disporre di un’officina o di una fabbrica di grandi dimensioni non è un requisito fondamentale per la prefabbricazione. Tutte le imprese possono iniziare con sistemi e lavori di piccola taglia, applicare procedure snelle e abbracciare queste innovazioni. Tutto ciò che serve è pianificare e pensare al futuro.
Il concetto di costruzione “intelligente” deve considerare anche la possibilità di una transizione dai metodi tradizionali a soluzioni basate su un sempre maggiore utilizzo di componenti standardizzati e prefabbricati. L’utilizzo del BIM consente lo sviluppo di un ambiente di progettazione e verifica intrinsecamente collaborativo che può accelerare l’adozione dell’approccio DfMA. È importante sottolineare che realizzare edifici in grado di offrire migliori prestazioni per l’intero ciclo di vita, di aumentare il livello di competenze nel settore e di sostenere lo sviluppo di tecnologie di produzione digitali e off-site, porterà anche alla realizzazione di edifici più sicuri e salubri.