I modular hospitals realizzati da Mangini Healthcare dispongono di un evoluto BMS sviluppato e customizzato da Kieback&Peter, che garantisce l’automazione di tutte le funzionalità impiantistiche necessarie a una terapia intensiva
di Fabrizio Corbe
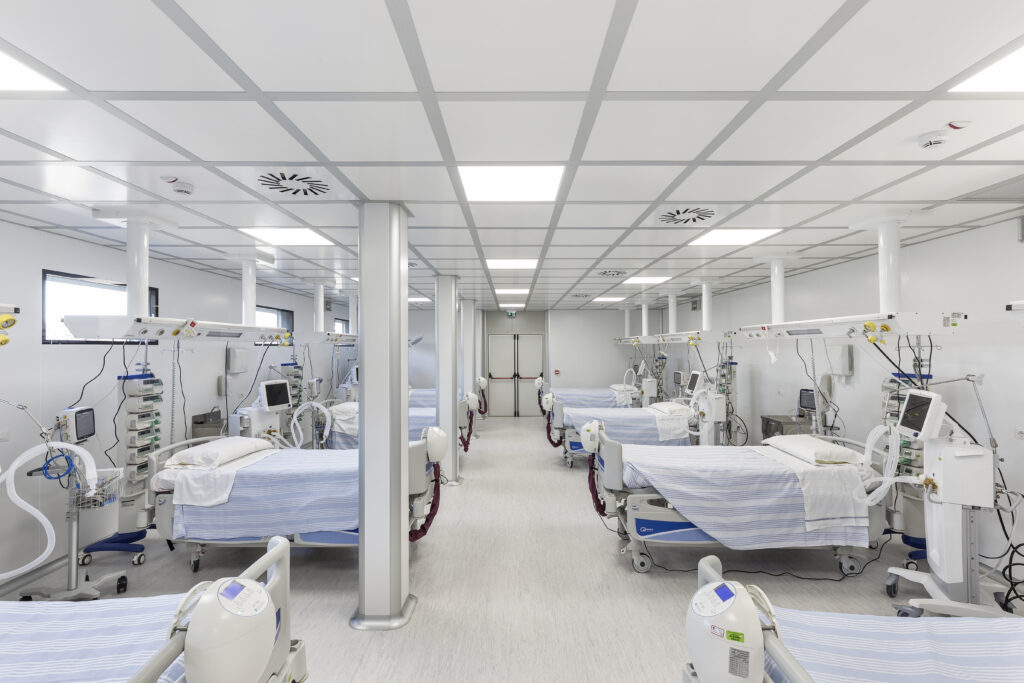
Attivato nel febbraio 2021, il Modular Hospital presso l’ospedale Sandro Pertini (ASL 2 di Roma) è stato ideato e costruito da Acotec Turnkey – divisione di Mangini Healthcare dedicata alla fornitura chiavi in mano di ambienti ad alto contenimento biologico. L’azienda ha poi realizzato altri modular hospitals presso gli ospedali San Giovanni Addolorata (Roma), G.B. Grassi (Ostia), Città di Castello (Perugia), San Giovanni Battista (Foligno) e San Salvatore (L’Aquila).
Realizzata in soli 54 giorni, la struttura presso l’ospedale Pertini accoglie 10 posti letto di terapia intensiva, all’interno di ambienti ampi circa 165 m2 caratterizzati da elevatissime prestazioni in termini di sicurezza, funzionalità, efficienza e affidabilità, grazie al sistema di regolazione, controllo e gestione messo a punto e fornito da Kieback&Peter in tempi ridottissimi.
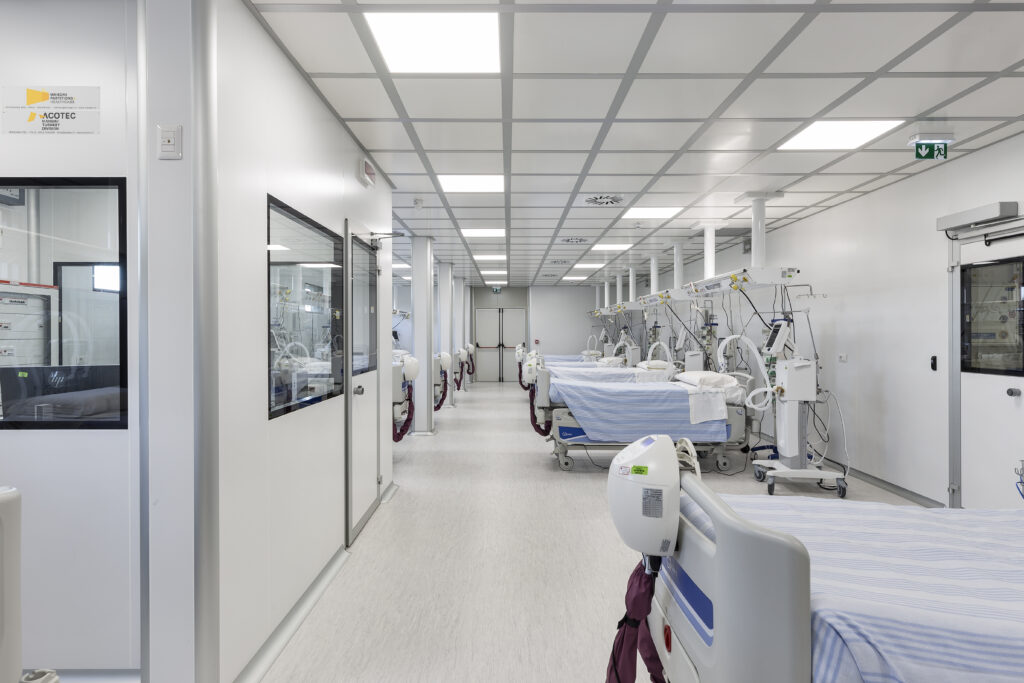
La qualità del BMS ha costituito un aspetto fondamentale per garantire le corrette condizioni ambientali ed evitare la diffusione degli agenti patogeni. Oltre alla fornitura del sistema, Kieback&Peter ha fornito tutti gli elementi in campo e i quadri di comando e controllo, fungendo da referente unico a livello tecnico.
Come è fatto il modular hospital
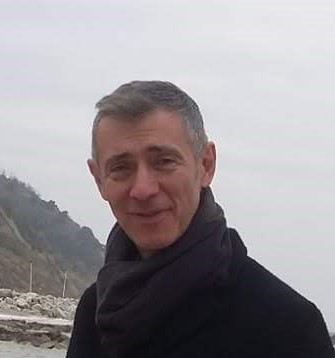
L’ing. Stefano Sarducci è Responsabile tecnico di Acotec Turnkey: «I nostri progetti sono destinati a diverse applicazioni nei settori farmaceutico, sanitario, microelettronico, aerospaziale, ecc.. In ambito ospedaliero, il concept dei modular hospitals è stato sviluppato per coprire una vastissima gamma di funzioni sanitarie, da quelle più semplici (ambulatori, fisioterapia, degenza ordinaria, ecc.) a quelle di tipo complesso (blocchi operatori, sale parto, pronto soccorso, terapie intensive, laboratori, diagnostica per immagini, ecc.)».
Quali sono gli aspetti tecnici più interessanti di un modular hospital? «A tutti gli effetti, i modular hospitals realizzati nell’ultimo anno per fronteggiare l’emergenza pandemica sono composti da ambienti a contenimento biologico. Si tratta di edifici prefabbricati concepiti per minimizzare i tempi di produzione e soprattutto di assemblaggio, che formano ambienti essenziali quanto funzionali. I componenti edili sono semplici, affidabili, estremamente performanti e dispongono di superfici anti-batteriche certificate. Ogni modular hospital è equipaggiato con impianti alimentati solo da energia elettrica e con tutte le apparecchiature medicali idonee alle terapie erogate. Ovviamente le funzioni ospedaliere critiche, come una terapia intensiva per pazienti infettivi, sono sistemi molto complessi, di conseguenza utilizziamo tecnologie performanti e affidabili per la gestione automatica del funzionamento, sviluppate e fornite da Kieback&Peter».
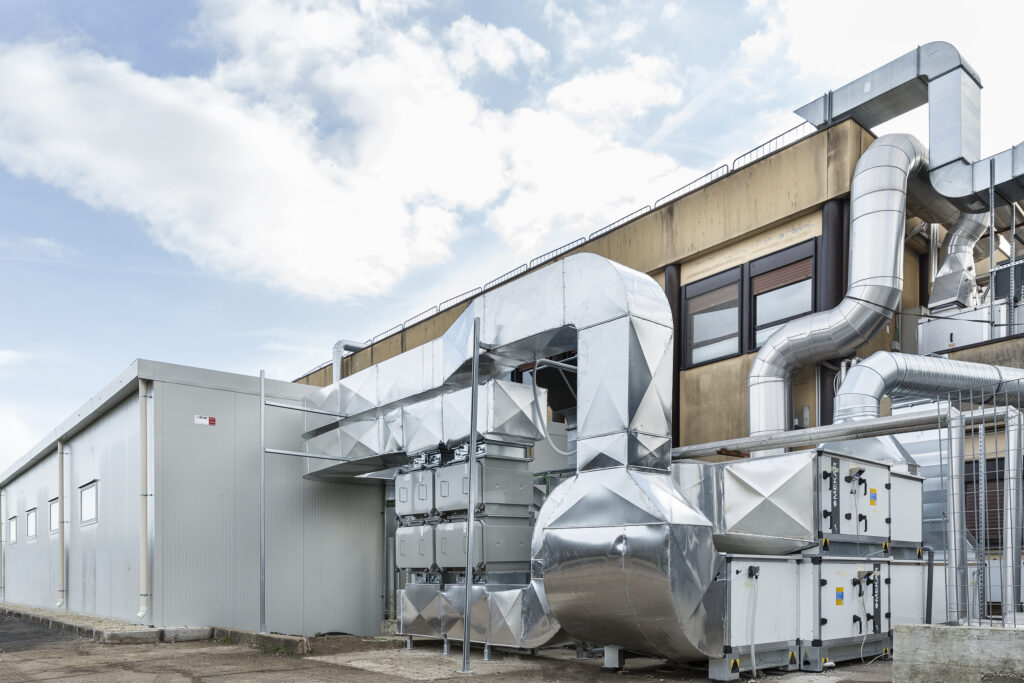
L’impianto HVAC
Nei modular hospitals i fluidi termovettori sono prodotti da una pompa di calore con modulo idronico e serbatoio di accumulo. L’impianto di ventilazione meccanica e climatizzazione è del tipo a tutt’aria esterna, attestato su una UTA e su un estrattore, che provvedono a:
– rinnovare l’aria senza ricircolo (nel caso del modular hospital presso l’Ospedale Sandro Pertini: mandata 3500 m3/h);
– filtrare l’aria immessa negli ambienti con filtri assoluti (H14);
– mantenere i diversi ambienti in adeguate condizioni di sottopressione rispetto all’ambiente esterno (-10 ÷ -15 Pa);
– climatizzare (T 20÷26 °C; U.r. 40÷60%) mediante le batterie calda-fredda e di post-riscaldamento e l’umidificatore a vapore elettrico;
– estrarre l’aria dalla terapia intensiva filtrandola con filtri assoluti (H14), attraverso doppio sistema canister (per la sostituzione in sicurezza dei filtri HEPA senza pregiudizio per la continuità del servizio).
A valle dell’UTA, la distribuzione dell’aria avviene tramite canalizzazioni in acciaio zincato isolate esternamente, con cassette a portata costante. Nella sala destinata ai pazienti, la diffusione dell’aria è affidata a diffusori a lancio elicoidale posti nella fascia centrale del controsoffitto, mentre l’estrazione è demandata a griglie poste in vicinanza delle pareti, in modo da innescare flussi d’aria che procedono dal connettivo centrale verso le testate dei letti.
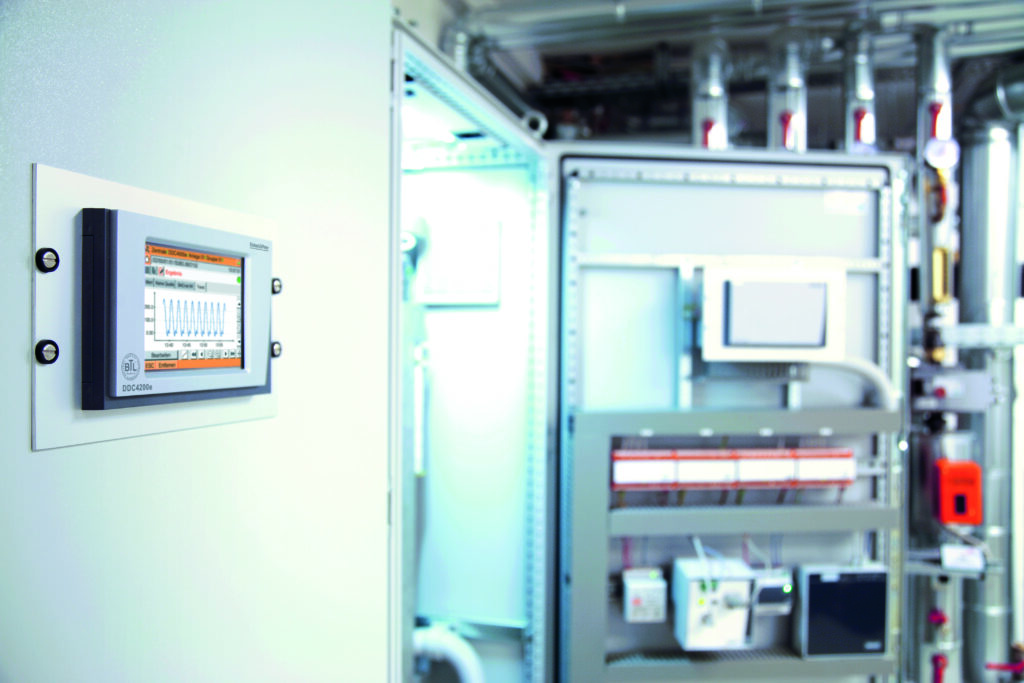
Applicazione ad alta complessità
Quali prestazioni sono richieste al BMS al servizio dei modular hospitals? «Oltre a creare le opportune condizioni di asepsi, qualità dell’aria e comfort negli spazi interni, a tutela della sicurezza e del benessere dei pazienti e degli operatori sanitari, ogni modular hospital garantisce anche il rispetto dei requisiti tipici di un edificio ospedaliero, ad esempio in termini di efficienza energetica, continuità d’esercizio, ecc.. Di conseguenza tutti i parametri significativi sono costantemente monitorati dal sistema, che si occupa di automatizzare il funzionamento di tutti gli impianti e di segnalare eventuali anomalie e malfunzionamenti, potendo anche dialogare con il sistema del committente. Poiché si tratta di un’applicazione ospedaliera ad alta complessità, che deve funzionare nel migliore dei modi con continuità, l’affidabilità è un requisito fondamentale per qualsiasi componente, compresa la centralina del BMS che è il vero e proprio “cervello” dell’impianto. Anche per questa ragione tutti i componenti critici, come l’estrattore d’aria, dispongono dell’alimentazione d’emergenza sotto UPS. Un’ulteriore caratteristica fondamentale – conclude l’ing. Sarducci – consiste nella possibilità di interagire con il BMS anche da remoto, per eseguire tutte le operazioni che possono essere effettuate sul posto, in modo da garantire la massima rapidità d’intervento – praticamente in tempo reale – anche a distanza».
Logica di funzionamento
L’avvio dell’estrattore precede sempre l’avvio dell’UTA e il funzionamento della pompa di calore è regolato in base alla domanda di riscaldamento o raffrescamento, con commutazione stagionale manuale. La corretta differenza di pressione è regolata a partire dal confronto tra le condizioni dei locali sporco e pulito e, successivamente, dalla serranda modulante di ripresa in base al set point stabilito.
La portata dell’aria di mandata è mantenuta costante in qualunque situazione, mediante regolazione del numero di giri dei ventilatori EC, in funzione della lettura della sonda in mandata.
La portata di aria estratta viene regolata, attraverso variazione del numero di giri del ventilatore EC, sulla base della misura di pressione sul canale di ripresa.
Per il controllo dell’umidità relativa, in fase di deumidificazione la regolazione della temperatura di saturazione è calcolata in funzione della media delle misure percepite dalle sonde poste sui canali di ripresa di alcuni locali di riferimento, mentre per l’umidificazione si agisce sul segnale modulante inviato all’umidificatore.
Oltre alla regolazione del microclima, un’altra funzione importante del sistema consiste nel monitoraggio, analisi e controllo dei dati. Queste funzioni sono fornite memorizzando nel tempo le misure di temperatura, umidità relativa e pressione ambiente, per poterle studiare al fine di ottimizzare le regolazioni.
In caso di malfunzionamento il sistema comunica una serie di allarmi, dal semplice avviso (filtro intasato) fino all’allarme critico di fermo macchina (in caso di anomalie del ventilatore o delle serrande) o di allarme pressione ambiente, con reset automatico o manuale e possibilità dell’invio di notifica all’operatore tramite e-mail, con più livelli di priorità.
Il BMS in sintesi
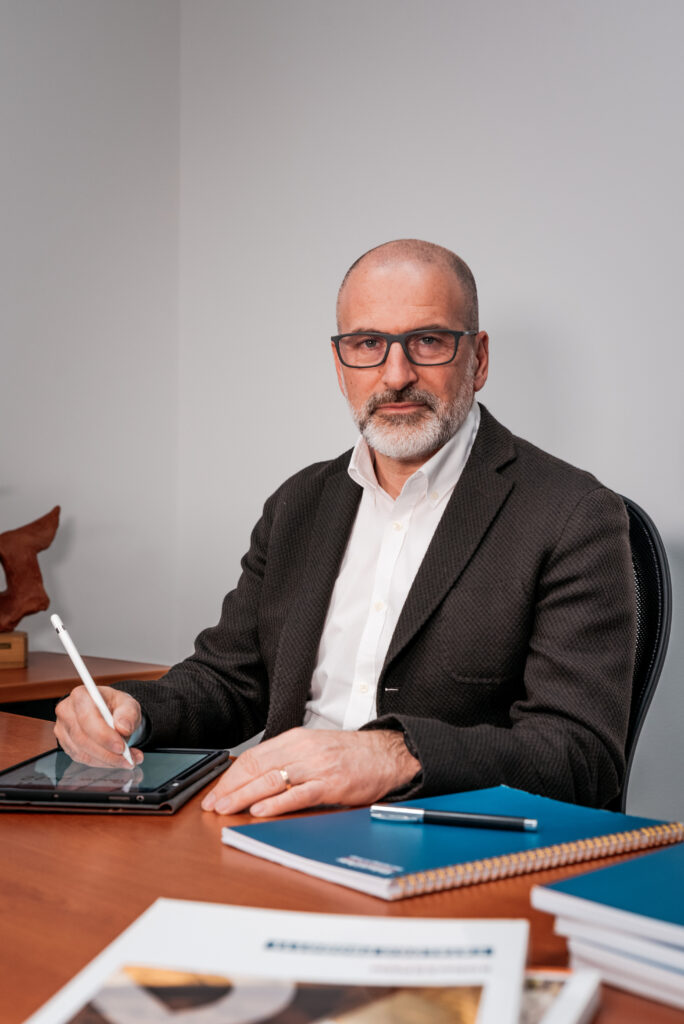
«La partecipazione alle commesse per i modular hospitals realizzati recentemente è la naturale conseguenza del rapporto di collaborazione esistente da tempo con Mangini Healthcare – afferma Roberto Rossi, Direttore Generale di Kieback&Peter Italia. Si tratta di edifici ospedalieri autonomi e completi dal punto di vista sanitario, oltre che autosufficienti sotto il profilo impiantistico e tecnologico.
Per questa ragione i modular hospitals sono equipaggiati con la nostra stazione di automazione DDC4200, riconosciuta dal mercato per l’efficienza e l’affidabilità, che utilizza protocolli BACNet TCP/IP costantemente aggiornati (BTL 1.20) per la massima integrazione con i sistemi esistenti, compresi quelli di terze parti. Anche se si tratta di un web server, la centralina permette l’esecuzione locale di tutte le funzioni di configurazione, controllo e gestione.
Abbiamo messo a punto un insieme di funzionalità e accorgimenti mirati alla realtà operativa dei modular hospitals, prevedendo ad esempio una gestione estremamente efficace e precisa per la regolazione delle pressioni differenziate all’interno dei singoli ambienti, oltre a soluzioni specifiche in termini di continuità del servizio (UPS, ecc.) e di ridondanza di alcune apparecchiature (ventilatori, ecc.).
Ci siamo anche occupati direttamente di tutte le dotazioni per supportare la proposta commerciale “chiavi in mano” di Mangini Healthcare, provvedendo sia alla progettazione e fornitura di tutti i sistemi e dispositivi necessari (quadri elettrici, sensori, valvole, ecc.), sia alla formazione delle figure professionali interessate a tutti i livelli nelle diverse fasi della commessa (progettazione, realizzazione, manutenzione).
Tutto questo rispettando i tempi strettissimi previsti dalle stazioni appaltanti per il completamento delle opere, nonostante le problematiche operative e le complessità verificatesi durante la prima fase della pandemia, ad esempio nel reperimento dei componenti».