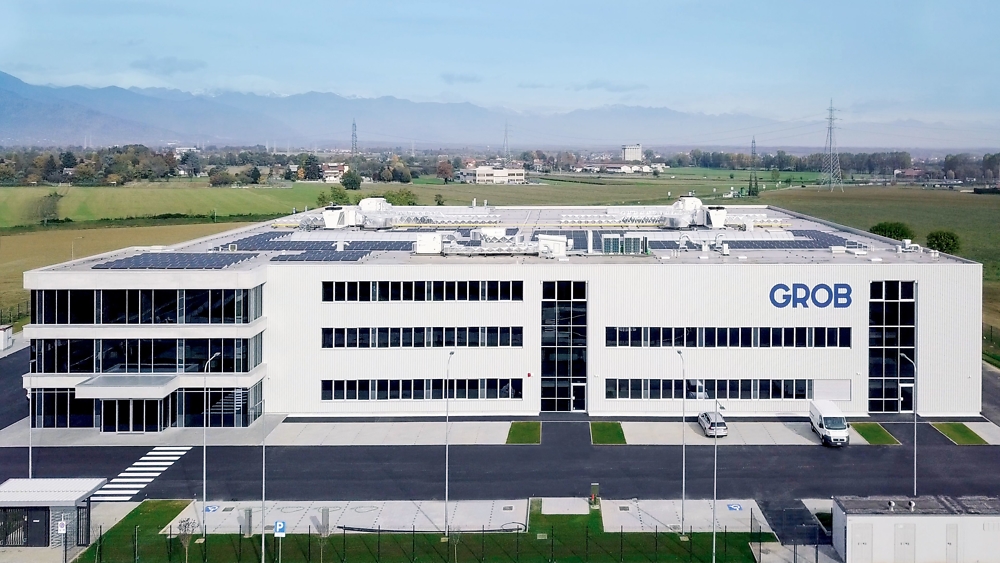
Efficienza energetica, flessibilità, contenimento dei consumi, comfort e qualità dell’aria indoor distinguono gli impianti a espansione diretta (VRF) realizzati presso lo stabilimento Grob Italy, utilizzando soluzioni sviluppate da Clivet.
Leader mondiale nella progettazione e produzione di macchine utensili e impianti destinati al settore della mobilità, il gruppo GROB ha completato nel 2020 il nuovo stabilimento a Pianezza (Torino), dedicato ai sistemi di produzione e automazione altamente innovativi per la nuova generazione di vetture elettriche. Oltre alla filiale italiana il gruppo dispone di altre quattro sedi produttive (l’headquarters a Mindelheim, Germania, e gli stabilimenti in USA, Brasile e Cina) più altre sedici succursali in tutto il mondo.
L’evoluto sistema di climatizzazione, che contribuisce in modo determinante alla classificazione energetica A1 dello stabilimento, è stato progettato dallo Studio Forgia Ingegneri Architetti Associati, che ha curato lo sviluppo impiantistico dell’edificio e l’adeguamento alle normative di prevenzione incendi. L’impiantistica è stata appaltata all’impresa TL Impianti (Torino). L’installazione degli impianti meccanici, basati su sistemi di condizionamento Clivet, è stata affidata all’impresa M.I.T. (Nichelino, Torino), con il contributo dell’agenzia Condsystem (Torino) e del centro assistenza AC Service (Moncalieri, Torino).
Edificio e impianti
Situato nella zona industriale (zona climatica E; 2.735 gradi giorno), lo stabilimento GROB Italy è costituito da un unico corpo di fabbrica (superficie circa 6.000 m2) posto al centro di un lotto ampio circa 15.000 m2, che comprende parcheggi e aree di manovra per gli automezzi pesanti circondati da spazi a verde. Realizzato con strutture portanti prefabbricate in calcestruzzo armato, disposte su 3 campate, l’edificio può accogliere circa 100 persone ed è articolato in due parti contigue e separate, destinate agli uffici (3 livelli fuori terra, con sale riunioni, spogliatoi e mensa del personale) e alla zona produttiva.
La climatizzazione è basata sull’impiego di soluzioni differenti e indipendenti, basati su un sistema VRF a pompa di calore con terminali tipo a ventilconvettori e unità dedicate all’aria primaria, negli spazi per uffici, e a tutt’aria, nell’area produttiva, con generatori termofrigoriferi ubicati sul tetto piano.
Gli impianti idrico-sanitari sono derivati dall’acquedotto cittadino: l’ACS è prodotta da pompe di calore Clivet modello SWAN 300 dotate di accumuli (ciascuno 300 l), con rete di alimentazione specifica per la mensa e relativi scarichi che convergono in un disoleatore. Due serbatoi interrati (ciascuno 15 m3) raccolgono le acque meteoriche riutilizzate per l’irrigazione dell’area verde.
Tutto lo stabilimento è protetto da una rete esterna di idranti UNI 70, alimentata da una stazione di pompaggio (pompa elettrica, motopompa, pompa jockey) con serbatoio interrato, più 12 idranti UNI 45 ubicati nell’area per uffici, collegati alla rete esterna con impianto a 4 colonne.
L’impianto elettrico è alimentato in MT tramite cabina esterna, che ospita 2 trasformatori da 630 kVA ciascuno. All’interno, la distribuzione in BT si attesta sul locale quadri elettrici generali al piano terreno, con quadri specifici di piano e di reparto rispettivamente per le aree uffici e produzione.
L’illuminazione artificiale è regolata con sistemi di controllo automatici, con una sezione di emergenza autoalimentata idonea a garantire la visibilità delle vie di fuga per almeno 1 ora. L’intero stabilimento è inoltre protetto dalla fulminazione con gabbia di Faraday collegata alla rete di terra. Sulla copertura è installato un impianto fotovoltaico da circa 121 kWp complessivi, composto da 362 moduli al silicio monocristallino (ciascuno 335 Wp) distribuiti in 4 sottocampi, ognuno attestato su inverter con potenza compresa fra 30÷40 kW.
La parola al progettista
L’ing Uberto Forgia (Studio Forgia Ingegneri Architetti Associati) ha curato la progettazione degli impianti meccanici ed elettrici/speciali:
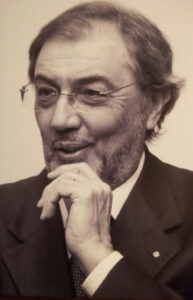
«La sfida principale è consistita nel garantire il comfort e benessere a tutto il personale, operai e impiegati, attraverso un impianto che fosse anche economicamente sostenibile. Rispetto a un tradizionale sistema idronico, composto da pompe di calore più caldaie a condensazione al servizio delle UTA, la soluzione basata su unità rooftop con tecnologia VRF ha restituito un impianto in grado di adattarsi meglio alle diverse esigenze dell’area produttiva e degli uffici.
L’impianto presenta infatti ingombri ridotti, è più semplice dal punto di vista distributivo e più flessibile. Inoltre gestione e manutenzione sono facilitate in quanto, durante gli eventuali periodi di sospensione invernale dell’attività dello stabilimento, non è soggetto a problemi di congelamento. Durante l’intero arco dell’anno è stato garantito il massimo del comfort termico e un’ottimale qualità dell’aria, in tutti gli ambienti dello stabilimento. In più è stato sfruttato al meglio l’impianto fotovoltaico installato sulla copertura, che copre circa il 30% dei consumi elettrici dello stabilimento con evidenti vantaggi anche economici».
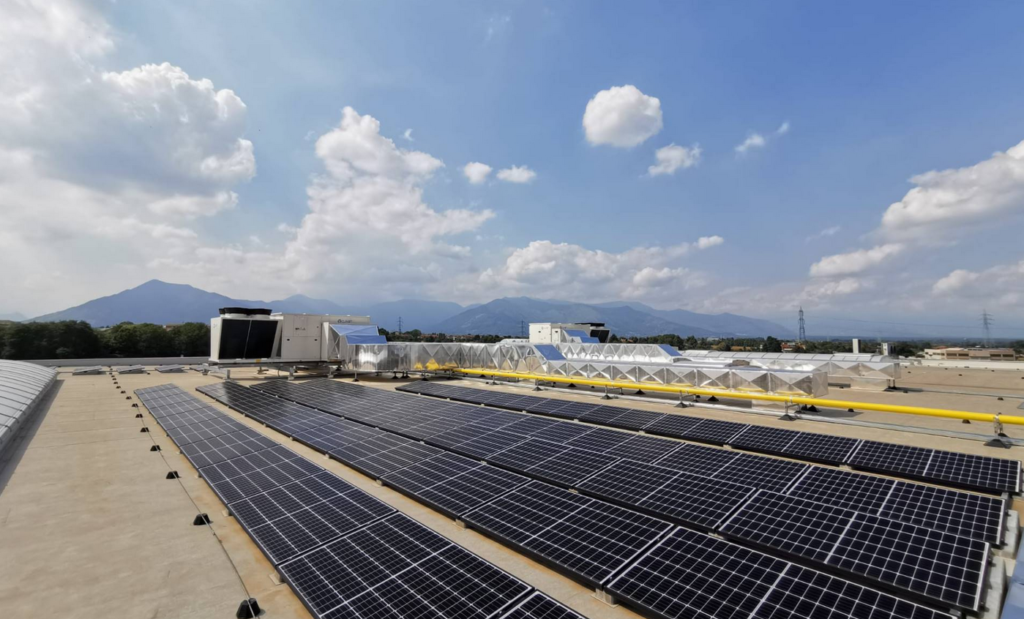
Clima e IAQ negli uffici
Le soluzioni impiantistiche per climatizzazione e ventilazione sono differenti a seconda della destinazione d’uso degli ambienti, ma tutti i generatori termofrigoriferi e le unità di trattamento dell’aria, di produzione Clivet, sono installate sulla copertura piana dello stabilimento, in prossimità degli spazi serviti.
La climatizzazione della zona per uffici (superficie totale circa 3.000 m2) è demandata a un sistema centralizzato VRF a pompa di calore, composto da:
- 5 unità esterne motocondensanti della linea VRF MV6-XMi (potenza compresa fra 14÷85 kW), del tipo ad alta efficienza dotate di compressore inverter DC (R410A), in grado di adattarsi in modo puntuale alle variazioni del carico;
- 96 ventilconvettori modello DZDF5-XMi, dei tipo carenato per installazione a pavimento, e modello Q4AN-2-XMI, da incasso a controsoffitto (per la hall), distribuiti nei diversi locali;
- tubazione in rame di andata/ritorno. Sempre nella zona per uffici, il ricambio igienico dell’aria è affidato a un impianto con funzionamento completamente indipendente e autonomo. Si tratta di 2 unità CPAN-XHE3 Zephir3 per il rinnovo igienico dell’aria, con recupero termodinamico attivo del calore in pompa di calore full inverter e la filtrazione elettronica ad alta efficienza (ISO 16890 ePM1 90%). Le unità sono destinate agli spazi di lavoro (9.500 m3/h) e alla mensa (4.400 m3/h).
Sono inoltre presenti 2 unità interne della linea IDU Heat Recovery (HRV) dedicate al rinnovo dell’aria e al recupero del calore dalle sale riunioni principali. Celate nei controsoffitti, le reti aerauliche sono realizzate con canalizzazioni in acciaio zincato a sezione rettangolare.
Rooftop per la produzione
Nella zona destinata ai processi industriali (circa 4.800 m2), climatizzazione e ventilazione sono demandate a 4 sistemi di tipo rooftop CSRN-XHE2 CLIVETPack2 80.4, ciascuno equipaggiato con:
- pompa di calore del tipo reversibile con compressori scroll (R410A) e condensazione ad aria (279 kWt con COP = 5,27; 285 kWf con EER = 4,29);
- modulo termico a condensazione (200 kWt) integrato, per la copertura del fabbisogno di picco nei periodi di basse temperature e il back-up della pompa di calore, alimentato da una rete di distribuzione del metano posata in esterni;
- configurazione a doppia sezione ventilante con aria di rinnovo (ciascuna 44.000 m3/h) e recupero termodinamico THOR (THermodynamic Overboost Recovery).
Grazie alle reti aerauliche in acciaio zincato a sezione rettangolare, le unità rooftop garantiscono il soddisfacimento dei carichi interni e il necessario ricambio igienico dell’aria, massimizzando il recupero dell’energia termica dall’aria esausta. Sono inoltre presenti 2 sistemi mini-VRF, al servizio dei locali tecnici situati nell’area produttiva, con relative motocondensanti installate in copertura.
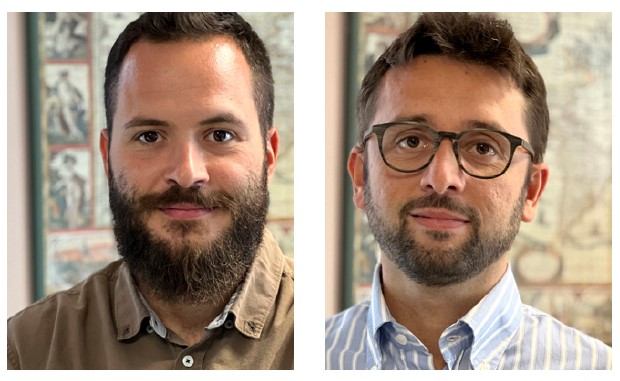
«Abbiamo ottenuto la commessa grazie alla collaborazione maturata negli anni con TL Impianti – afferma l’ing. Luca Teoldi, Project manager dell’impresa M.I.T. – che ci ha affidato la realizzazione degli impianti (climatizzazione, idrico sanitario, antincendio e aria compressa, più il laboratorio metrologico). Sono state attivate numerose professionalità interne, fra cui il team di progettisti, l’ufficio tecnico e soprattutto il nostro personale altamente qualificato. Il nostro standard organizzativo prevede sempre la partecipazione del gestore di commessa, del direttore tecnico di cantiere e delle figure tecniche di supporto alla progettazione costruttiva e al controllo della sicurezza. Personalmente mi sono occupato della gestione organizzativa ed economica della commessa, affiancato dai responsabili tecnici e dal capocantiere per la gestione delle maestranze interne e dei subappaltatori».
Secondo quali criteri avete selezionato i principali componenti impiantistici?
«Nella scelta delle pompe di calore, delle unità rooftop e dei terminali in ambiente ventilconvettori abbiamo puntato sui prodotti Clivet – spiega l’ing. Marco Piovano, Responsabile dell’Ufficio Tecnico di M.I.T. Si tratta di un’azienda presente sul mercato da oltre 30 anni, leader a livello europeo per gli impianti di climatizzazione e, in particolare, per i sistemi ad espansione diretta. Ci siamo affidati alla competenza e all’esperienza di Clivet e la scegliamo come partner in quanto, con un ottimo rapporto qualità-prezzo, riusciamo a rispondere alle esigenze dei nostri clienti finali».
Come vi siete organizzati per le attività di installazione?
«Il cantiere è durato 10 mesi – riprende Luca Teoldi – durante i quali siamo stati presenti in media con 14 persone impiegate nella realizzazione degli impianti meccanici. La tempistica concessa non lasciava molto margine, ma grazie all’esperienza di tutte le figure coinvolte e alla reciproca collaborazione tra imprese e progettisti, siamo comunque riusciti a fronteggiare anche gli adeguamenti al progetto intervenuti in corso d’opera, necessari per alcune modifiche richieste dal cliente. Siamo perciò molto soddisfatti del risultato ottenuto».