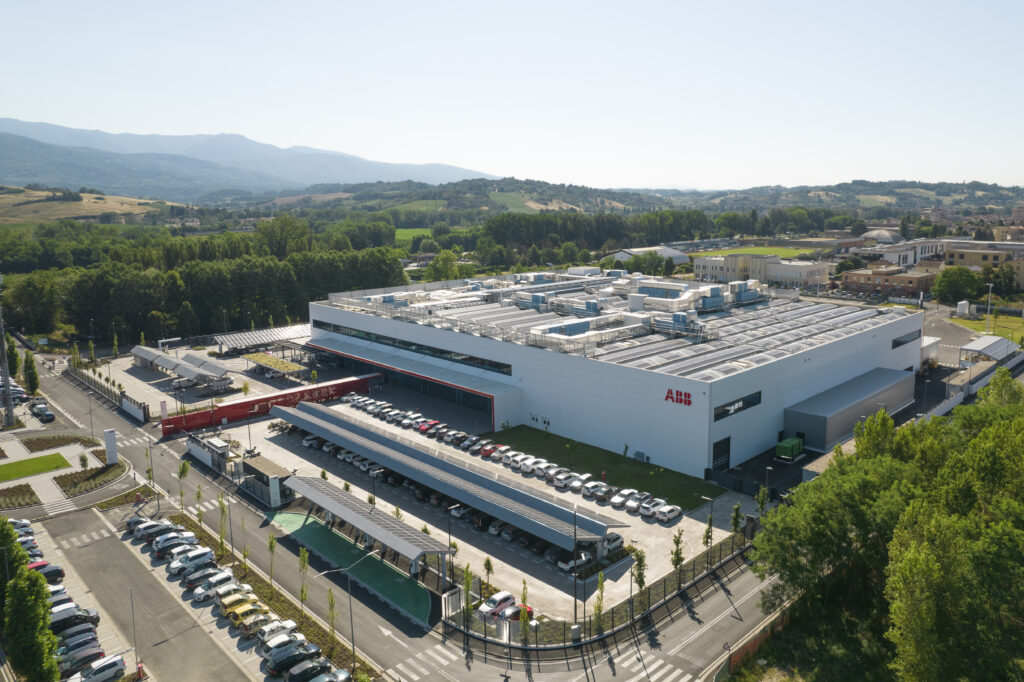
Il nuovo stabilimento ABB e-mobility di San Giovanni Valdarno dispone di impianti di climatizzazione a tutt’aria che coniugano efficienza energetica, sostenibilità e ottimali condizioni di comfort e salubrità per circa 500 persone.
Entrato in funzione nel novembre 2021, lo stabilimento è il più grande sito produttivo italiano del gruppo ABB destinato alla produzione di stazioni di ricarica in corrente continua – un vero e proprio centro di eccellenza per ricerca e sviluppo, progettazione, ingegnerizzazione e produzione di sistemi di ricarica per qualsiasi tipo di veicolo alimentato con batterie elettrochimiche.
Lo stabilimento è risultato di un investimento di 30 milioni di dollari e costituisce un importantissimo passo in avanti per l’elettrificazione di tutti i settori del trasporto pubblico e privato. La capacita produttiva del gruppo raggiunge cosi le 10.000 stazioni di ricarica all’anno, con prodotti alta gamma come Terra 360 – la stazione DC che puo garantire una ricarica di 100 km in soli tre minuti.
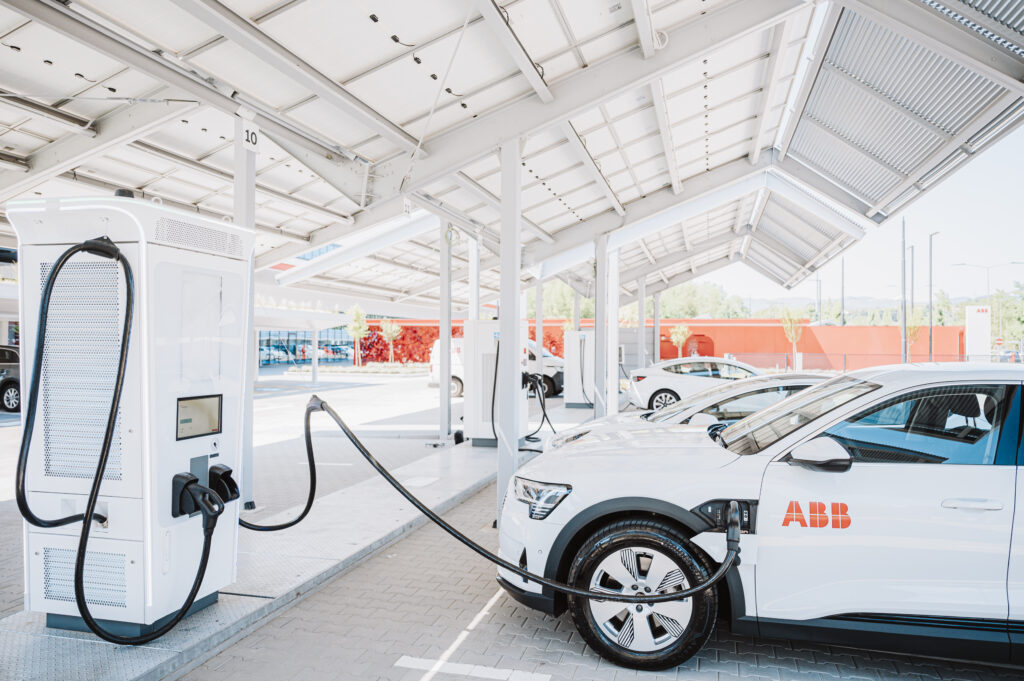
Realizzato secondo principi eco-sostenibili, l’edificio sarà certificato LEED rating Gold e, come tutti i siti ABB italiani, utilizza esclusivamente energia da fonte rinnovabile certificata, con il contributo aggiuntivo di un campo fotovoltaico da circa 600 kWp installato sulla copertura e sulle pensiline dei parcheggi (in luogo dei 217 kWp imposti dalle normative), per una produzione totale annua stimata in 720 MWh.
L’edificio in sintesi
Lo stabilimento sorge nella zona industriale a nord del centro abitato, all’interno di un’area pianeggiante ampia circa 45.000 m2, di cui circa 16.000 m2 occupati dal volume parallelepipedo dell’edificio. Identificato da ampie superfici trasparenti, l’ingresso principale è rivolto a settentrione, preceduto da due aree a parcheggio di cui quella interna dispone di 82 stazioni di ricarica del tipo AC e DC ed è già predisposta per accogliere fino a 192 chargers.
Parte dello stabilimento è a tutta altezza (circa 12 m), mentre il resto e articolato su due livelli, entrambi distinti da un’elevata flessibilità spazio-funzionale. Al piano terreno si trovano hall d’ingresso, area ristorazione (cucina, mensa, bar con dehors ombreggiato), spogliatoi, reparti produttivi (assemblaggio, finitura e personalizzazione, innovazione di prodotto, ecc.), la zona R&D e i magazzini (componenti, prodotti finiti, ecc., con l’area di carico-scarico). Il reparto R&D, in particolare, è ampio circa 3.200 m2 e accoglie una settantina di tecnici altamente specializzati.
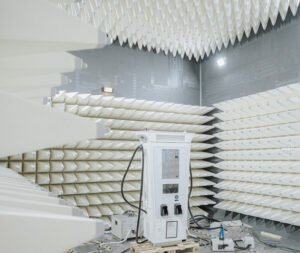
Al piano terreno comprende camera anecoica, camere climatiche con ΔT da -40 a +85 °C (di cui una con alta velocita di rampa, che utilizza azoto liquido per il raffreddamento rapido), laboratori per i controlli di compatibilità elettromagnetica, ecc., per complessive 15 aree di test in grado di simulare oltre 400 sessioni di ricarica al giorno; al piano superiore si trova invece l’area engineering.
Al piano superiore si trovano altre superfici produttive e gli uffici, con sale riunioni affacciate verso un patio a cielo aperto. La centrale termica, idrico-sanitaria e di trattamento dell’aria sono situate sulla copertura condivisa con il campo fotovoltaico. Un’altra area a vocazione impiantistica, dedicata ai test sui prodotti, e situata al piano terreno all’esterno della zona R&D.
Efficienza, salubrità, comfort
L’intero stabilimento e equipaggiato con un impianto a 4 tubi, che utilizza principalmente reti di ventilazione a tutt’aria in grado di restituire significativi vantaggi dal punto di vista energetico, igienico-sanitario, della flessibilita d’installazione e della pressoche totale assenza di terminali idronici in ambiente. La sostenibilità energetica degli impianti di climatizzazione è ottenuta attraverso l’impiego di generatori termici e frigoriferi caratterizzati da prestazioni ai vertici della categoria ed effettuando sempre, ove possibile e conveniente, il recupero termico sia sui generatori stessi, sia del calore contenuto nell’aria esausta.
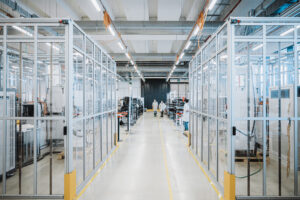
In alcuni ambienti – ad esempio nel reparto di lavorazione delle schede elettroniche, che necessitano di un processo di verniciatura – era necessario effettuare un completo ricambio dell’aria. In questo caso le canalizzazioni di ripresa sono state inserite nella linea di produzione, anche per evitare la diffusione degli odori, e previa filtrazione convergono verso il recuperatore di calore dell’UTA dedicata, prima dell’espulsione in atmosfera.
Negli altri ambienti con necessita di volumi di ricambio inferiori, è stato comunque deciso di maggiorare gli impianti aeraulici per permettere il ricambio dell’aria al 100%, in modo da minimizzare il rischio per il personale nei periodi critici dal punto di vista sanitario.
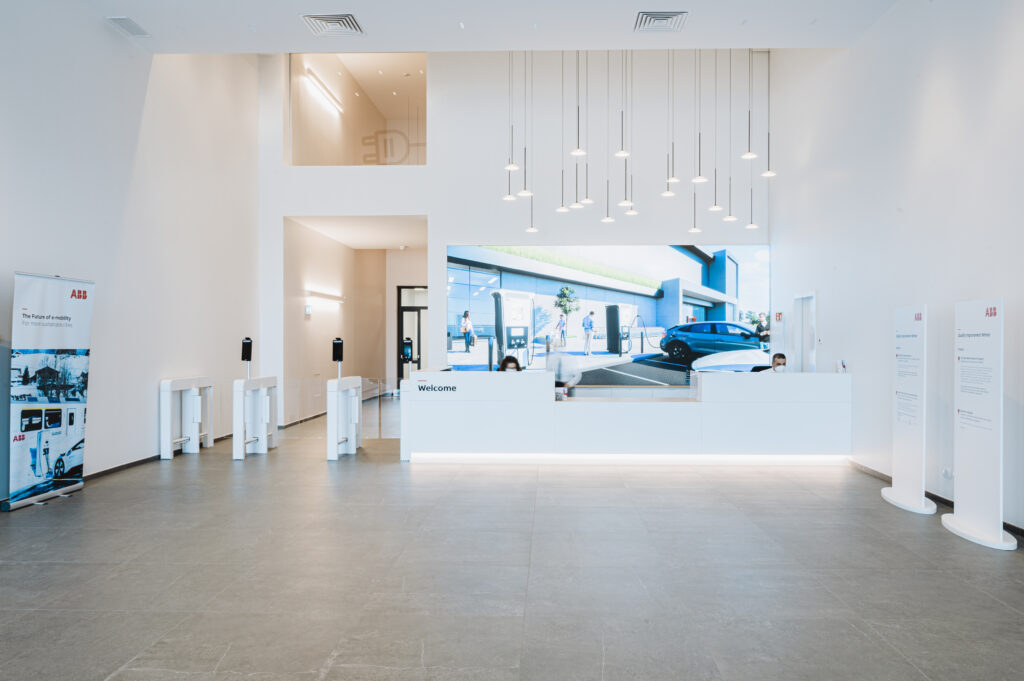
Per evitare che i virus patogeni possano proliferare grazie ai microorganismi presenti nell’aria, nelle UTA è stata prevista la possibilità di installare filtri con funzione battericida. Il posizionamento in copertura delle centrali termofrigorifere e delle UTA – queste ultime, in particolare, sono distribuite in prossimità dei cavedi tecnici al servizio delle diverse zone dello stabilimento – ha permesso di minimizzare la lunghezza delle reti e le conseguenti dispersioni termiche.
Le reti degli impianti aeraulico e antincendio, al pari di quelle degli impianti elettrici e speciali, occupano la fascia superiore degli ambienti. Le superfici a pavimento risultano perciò libere da qualsiasi vincolo impiantistico e permettono modifiche rapide in caso di cambiamenti al layout spazio-funzionale.
L’ottimizzazione del funzionamento degli impianti (regolazione termica, trattamento dell’aria, illuminazione artificiale, ecc.) è affidata al BMS sviluppato, prodotto e ingegnerizzato da ABB. Con circa 9.000 dispositivi che permettono la gestione di circa 34.000 variabili, la piattaforma è attiva praticamente in ogni zona dell’edificio e mette a disposizione un potenziale di risparmio energetico nell’ordine del 60% rispetto alle soluzioni tradizionali.
Oltre alla funzioni tipiche connesse alla supervisione, regolazione e controllo dei sistemi tecnologici dell’edificio realizzate con diversi protocolli (ModBus, BacNet, eConnex, DALI, ecc.), la piattaforma si occupa anche della gestione dei sistemi di ricarica attraverso un modulo dedicato, che utilizza il protocollo aperto OCPP specifico per la comunicazione tra punti di ricarica e sistema centrale.
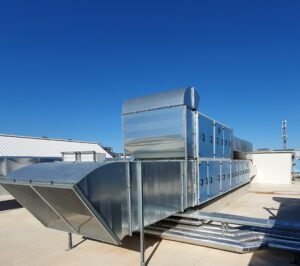
Nell’intero stabilimento la climatizzazione è affidata a una rete di ventilazione del tipo a tutt’aria, attestata su 18 UTA tutte con possibilità di funzionamento in free cooling ed equipaggiate con:
- presa dell’aria esterna con serranda;
- silenziatori a setti;
- recuperatore di calore a flussi incrociati (solo per le UTA dedicate a uffici logistica e sala riunione NPI);
- recuperatore di calore idronico a batteria con rendimento 85% (per tutte le altre UTA); – ventilatori del tipo plug fan con inverter;
- filtri di tipo G3 (per unità interne), G4 + F8 (per unità esterne), G4 + F7 (per recuperatori di calore);
- batterie per riscaldamento, raffrescamento-deumidificazione, postriscaldamento;
- umidificazione a nebulizzazione ultrafine ad alta pressione;
- canale ed espulsione dell’aria con serranda.
Complessivamente i volumi dell’aria trattati sono nell’ordine di 422.800 m3/h, di cui 127.500 m3/h per l’aria primaria in mandata e 378.300 m3/h per la ripresa, a fronte di un ricambio minimo dell’aria garantito nell’ordine di 6,5 l/s per persona (23,4 m3/h) negli spazi produttivi e di 10 l/s (36 m3/h) in uffici, spogliatoi e mensa. In ogni stagione la temperatura ambiente può essere modificata in funzione alla temperatura esterna.
La distribuzione dell’aria è realizzata per garantire che il flusso immesso nei locali si misceli convenientemente con l’aria ambiente, in tutto il volume convenzionale occupato. La velocità terminale nella zona occupata è calcolata per non essere superiore a 0,15÷0,25 m/sec. Negli spazi produttivi mandata e ripresa sono realizzate con canalizzazioni ramificate a sezione rettangolare, realizzate con pannelli sandwich.
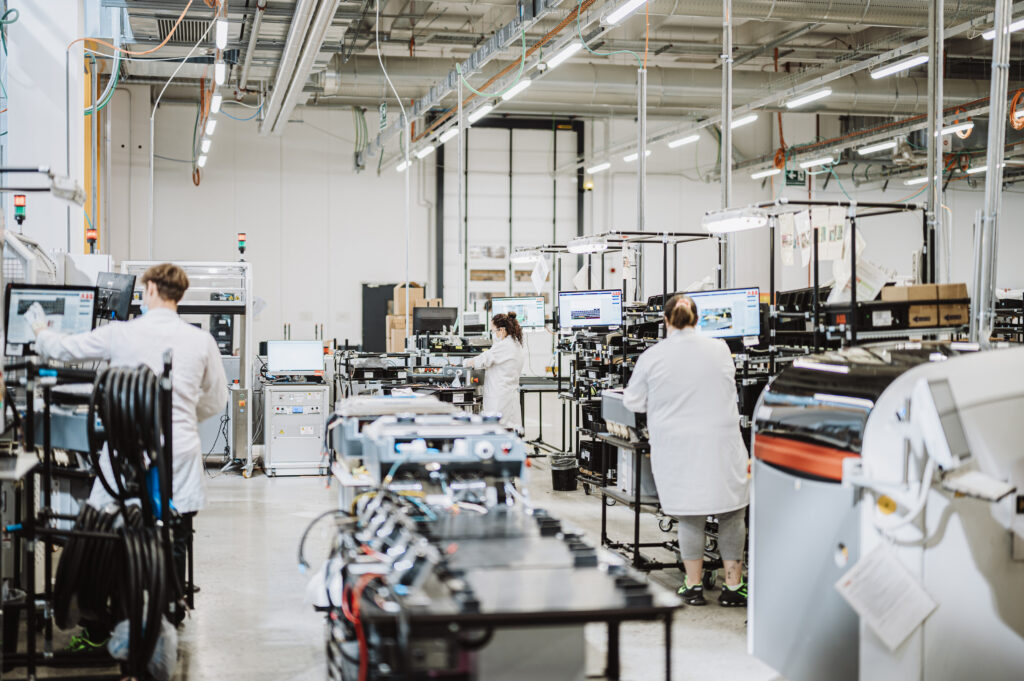
L’immissione in ambiente avviene attraverso canali del tipo microforato a sezione circolare, in acciaio, per facilitare la diffusione dell’aria verso il basso, uniformare la temperatura negli ambienti con altezza elevata ed evitare così la stratificazione. Negli uffici e sale riunioni l’aria è immessa attraverso i controsoffitti, mediante travi a induzione, con ripresa affidata a diffusori a griglie. In questi ambienti il controllo climatico può essere regolato localmente, grazie a regolatori di portata dell’aria e alle batterie di post-riscaldamento.
Nel magazzino sono presenti aeroconvettori a soffitto, che provvedono al ricircolo dell’aria operando il riscaldamento o raffrescamento a seconda delle necessità. Negli spogliatoi l’aria è immessa attraverso i controsoffitti, mediante diffusori del tipo puntuale, ad alta induzione, con ripresa mediante diffusori a griglie. La cucina è equipaggiata con una cappa per l’estrazione forzata dall’aria, equipaggiata con ventilatore e motore resistenti fino a 110 °C, con compensazione affidata all’UTA dedicata.
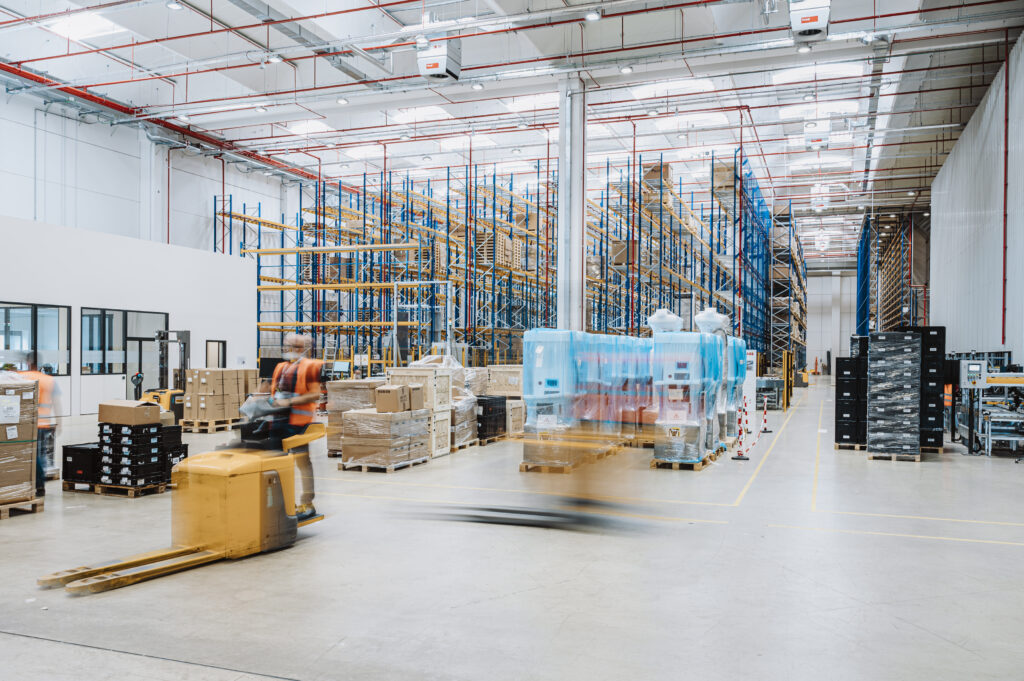
Tutte le canalizzazioni di ripresa, comprese quelle provenienti dalle aspirazioni dei servizi igienici, convergono verso i recuperatori di calore delle UTA. Gli unici punti di espulsione dell’aria non soggetti al recupero del calore sono situati sulla copertura, in corrispondenza dei forni per la saldatura e per l’essiccazione della vernice.
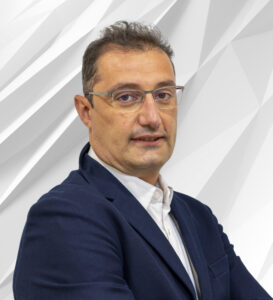
«Lo stabilimento di San Giovanni Valdarno è un edificio d’eccellenza sotto il profilo della qualità architettonica, energetica e ambientale, che esprime appieno i valori del gruppo ABB anche attraverso un’immagine coerente con la brand identity. L’obiettivo era realizzare un fabbricato in classe energetica A realizzato solo con materiali certificati.
Per ottenere un involucro edilizio adeguatamente termoisolato abbiamo dapprima selezionato sistemi costruttivi e materiali termoisolanti fra i più efficaci, abbattendo così il fabbisogno termico e frigorifero necessario alla climatizzazione. Nel caso dell’isolamento delle pavimentazioni industriali – alcune delle quali sono chiamate a sopportare carichi notevoli – la ricerca di un materiale in grado di garantire anche elevate prestazioni dal punto di vista statico (700 kPa per il magazzino; 500 KPa per lo stabilimento) ha condotto all’impiego di polistirene estruso espanso (spessore 20 cm). Per l’isolamento delle coperture, invece, la lana minerale (10 cm) è stata utilizzata per motivi di sicurezza antincendio connessi alla presenza dell’impianto fotovoltaico.
L’involucro verticale e realizzato con pannelli prefabbricati ed è volutamente molto trasparente, ben oltre i minimi normativi, in modo da creare condizioni di abbondante illuminazione naturale anche degli spazi a vocazione produttiva».
Quali criteri hanno guidato il progetto degli impianti meccanici?
«Le scelte operate per la climatizzazione sono risultato di un concept finalizzato alla massima efficienza energetica, attraverso un’attenta valutazione delle caratteristiche e delle performances dei diversi materiali e tecnologie utilizzati, anche dal punto di vista delle esigenze produttive.
Le centrali termofluidiche e di trattamento dell’aria sono tutte situate sulla copertura, al duplice scopo di minimizzare la lunghezza delle reti – e, perciò, anche le dispersioni termiche – e di separare fisicamente l’area tecnologica dal resto dello stabilimento che, in questo modo, dispone di spazi esterni quasi esclusivamente dedicati alla produzione.
La compresenza di generatori termofrigoriferi e a combustione assicura sia un elevato grado di efficienza, in relazione alle condizioni meteorologiche esterne, sia la massima continuità operativa dello stabilimento, chiamato a lavorare a pieno regime durante l’intero arco dell’anno. La selezione delle unità per il trattamento dell’aria è stata orientata dalla volontà di utilizzare macchine in classe A+ e in grado di garantire le migliori condizioni igienico-sanitarie dell’aria.
Le superiori prestazioni termoisolanti dei pannelli di rivestimento delle UTA e la possibilità di impiegare filtri battericidi hanno ristretto la cerchia dei potenziali fornitori. Negli spazi interni, l’impiego di terminali ad alta induzione elimina la stratificazione termica a vantaggio del comfort. Oltre alla volontà di perseguire il massimo grado di efficienza energetica, anche a vantaggio del punteggio ottenibile per la certificazione LEED, l’impiego di un BMS pervasivo assolve anche all’importante compito di facilitare l’individuazione di anomalie e malfunzionamenti, consentendo la programmazione degli interventi di manutenzione e mantenere così un elevato indice di produttività dello stabilimento».
Centrale termofluidica e impianti indipendenti
Il fabbisogno termico e frigorifero dello stabilimento è pari a circa 3.200 kWt e a 3.900 kWf, più circa 100 kWt per la produzione dell’ACS. La produzione dei fluidi per la climatizzazione è affidata a:
- 2 pompe di calore aerotermiche (ciascuna da 850kWt ; 850 kWf), equipaggiate con 14 compressori scroll (R410A) e 4 circuiti l’una;
- 2 chiller (ciascuno 1.100 kWf), equipaggiati con 2 compressori a vite (R134A);
- 4 caldaie a condensazione (ciascuna 350 kWt); I chiller, in particolare, sono dotati di doppio circuito frigorifero e sono caratterizzati da elevati standard di efficienza (EER 3.05, SEER 5.25).
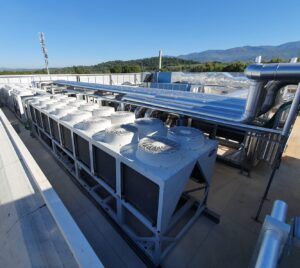
I desurriscaldatori al servizio dei chiller mettono a disposizione circa il 20% della potenza nominale dei gruppi frigoriferi per la produzione dei fluidi tecnici. In estrema sintesi, la logica di funzionamento della centrale termofrigorifera prevede che:
- nel periodo estivo si attivano dapprima i chiller e poi le pompe di calore, con modalità in cascata;
- nel periodo invernale, con una temperatura esterna superiore a ~7 °C, si attivano prima le pompe di calore, mentre con temperatura esterna inferiore alla stessa soglia si accendono prima le caldaie.
I fluidi sono prodotti alle seguenti temperature:
- 50 °C (caldaie) con ΔT 50÷40 °C;
- 45 °C (pompe di calore) con ΔT 45÷40 °C;
- 7 °C (gruppi frigoriferi e pompe di calore) con ΔT -7÷12 °C.
A valle dei generatori i fluidi sono stoccati in 3 serbatoi (2 da 5.000 l per acqua refrigerata; 1 da 5.000 l per acqua calda) e quindi inviati alle batterie delle UTA e agli altri circuiti secondari.
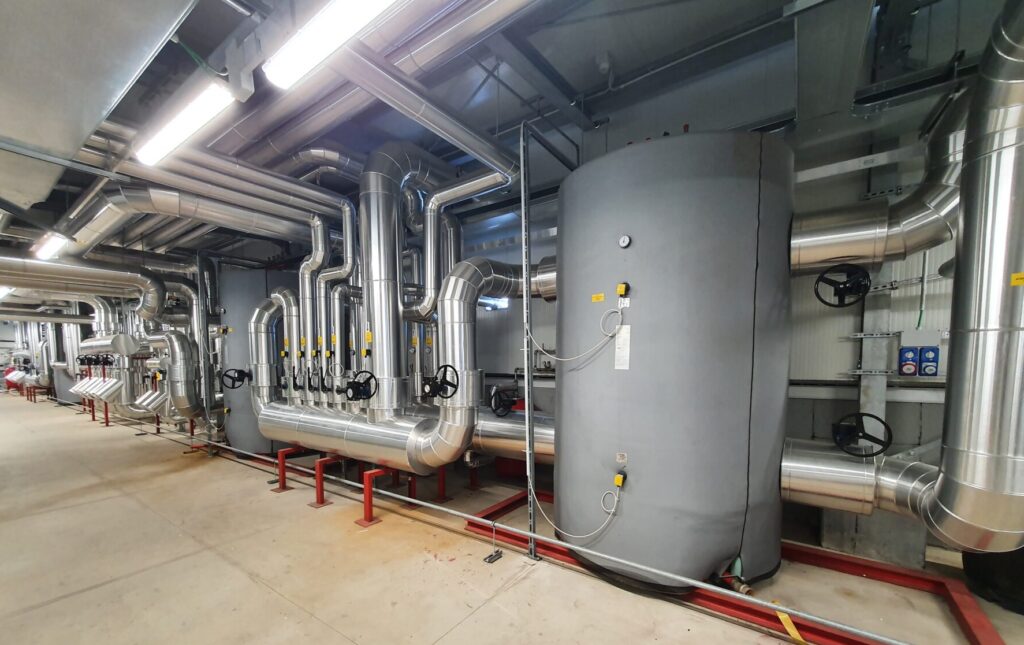
Lo stabilimento dispone anche di impianti di climatizzazione indipendenti, al servizio delle zone destinate a:
- sistemi IT, raffreddati da un impianto di condizionamento a espansione diretta, opportunamente ridondante;
- forno di processo, mediante 2 chiller con funzionamento indipendente e ridondante che alimentano uno scambiatore di calore;
- simulazione di batteria nella zona R&D.
Quest’ultima e dedicata ai test sui prodotti ed e composta da un locale equipaggiato con torrini di ventilazione dotati di serrande, che nel periodo invernale operano il raffrescamento naturale mediante estrazione e ricambio con l’aria esterna e gruppi frigoriferi a espansione diretta per ottenere il raffreddamento estivo.
Altri impianti meccanici
L’idrico-sanitario è attestato sul punto di consegna dell’acquedotto pubblico. L’acqua raggiunge la centrale in copertura, che dispone di serbatoi per acqua calda e fredda (ciascuno 2.000 l); la distribuzione a tutto lo stabilimento avviene tramite autoclave.
Nella centrale si effettuano i seguenti trattamenti:
- addolcimento dell’acqua (7÷10 °F) per usi potabili, di processo e tecnologico mediante addolcitore automatico a scambio ionico, a singola colonna con rigenerazione volumetrica pura, con programma multifunzione in grado di gestire il sistema di autodisinfezione preceduto da filtrazione;
- addolcimento dell’acqua (7 °F) per la sola cucina, con sistema dalle caratteristiche simili al precedente;
- antilegionella per la produzione dell’ACS, con aggiunta di additivi polifosfati e dosaggio di prodotti sanitizzanti e biocida a base di perossido di idrogeno e sali di argento.
Nel periodo estivo l’ACS è prodotta principalmente da 2 pompe di calore (ciascuna 16 kWt) e da una caldaia a condensazione (100 kWt), con logica di funzionamento differente in relazione alla temperatura esterna (simile a quella utilizzata per la climatizzazione). Il bollitore (2.000 l) provvede alla preparazione finale.
Le reti di distribuzione idrico-sanitaria sono realizzate in tubazioni in acciaio zincato, per le dorsali, e in multistrato, per i servizi igienici e docce, che alimentano apparecchi erogatori dell’acqua con funzionamento automatico, installati su sanitari realizzati con porcellana autopulente. Le reti di scarico sono realizzate con tubazioni in polipropilene dotate di sifoni e ventilazione primaria e secondaria, con raccolta separata delle acque oleose rispetto a quelle reflue. Le reti di raccolta dell’acqua piovana confluiscono verso una vasca di recupero (50.000 l) per l’irrigazione delle aree verdi. Per ragioni di sicurezza connesse alle specificità dei prodotti e di alcune delle operazioni, che prevedono l’impiego di elettricità, nello stabilimento sono state previste soluzioni ad hoc per l’impianto antincendio.
In generale, gli ambienti sono protetti da un impianto sprinkler, alimentato con acqua addizionata a schiumogeno concentrato per aumentare la capacità estinguente, e da impianti a gas inerte. Nel primo caso la rete è attestata sulla centrale antincendio (elettropompa, motopompa, pompa jockey), che utilizza una riserva d’acqua (646 m3) proveniente dalle vasche di riserva. La miscela è veicolata fino alle testine mediante tubazioni in acciaio che si ramificano nelle varie zone dello stabilimento.
Gli impianti a gas sono al servizio del centro servizi IT e del magazzino automatico verticale. Prendono origine da una centrale a bombole riempite con gas ecologico (fluoroketone-C6), che non necessita di completa saturazione dell’ambiente per l’estinzione dell’incendio, a garanzia della sicurezza del personale.
Per le esigenze produttive è inoltre presente una centrale di compressione dell’aria equipaggiata con 2 compressori rotativi a vite azionati tramite inverter e motore elettrico a magneti permanenti raffreddato ad olio, che mettono a disposizione una portata complessiva di 2,94÷18,36 m3/min con pressione massima pari a 7 bar.