Il controllo in continuo della carica delle apparecchiature frigorifere rappresenta una strategia fondamentale non solo per garantire la sicurezza di impiego, ma anche per ridurre i costi di gestione e allungare la vita delle centrali termofrigorifere.
Le restrizioni imposte dal nuovo regolamento europeo sugli F-Gas provocheranno nei prossimi anni un aumento esponenziale del costo da affrontare per la ricarica delle apparecchiature frigorifere in caso di perdite. Inoltre, comporteranno un sempre maggiore impiego di refrigeranti con caratteristiche di infiammabilità, sia naturali come il propano, sia sintetici come gli HFO in classe A2L, con le conseguenti problematiche di sicurezza. Infine, il processo di elettrificazione in atto, con la relativa adozione di gruppi frigoriferi a pompa di calore per il riscaldamento degli ambienti, rende assolutamente imperativa la necessità di garantire la continuità di funzionamento, evitando i fermi per guasto in modo da non compromettere la fruizione degli spazi abitati.
Diventa quindi ancor più necessario fare in modo che le perdite di gas siano ridotte al minimo adottando idonei sistemi di rilevamento in continuo di tipo fisso, finora ancora poco conosciuti e utilizzati. La maggior parte dei rilevatori attualmente specificati per le apparecchiature frigorifere dagli standard di sicurezza forniscono livelli grossolani di prevenzione essendo in grado di individuare soltanto fughe di gas di grande entità, mentre sono inefficaci nel fornire un allarme tempestivo delle perdite più ridotte.
I sistemi di monitoraggio del tipo ad alta sensibilità rappresentano invece la soluzione ottimale per ottenere sia la sicurezza degli occupanti che il rilevamento immediato delle perdite che consentono riduzione delle emissioni, risparmio sui costi, miglioramento della manutenzione e massima efficienza e continuità operativa delle centrali frigorifere o, per meglio dire, termofrigorifere dato che ospitano ormai comunemente pompe di calore per il riscaldamento degli ambienti e la produzione di acqua calda sanitaria (figura 1).

Il nuovo regolamento F-Gas
La riduzione delle emissioni di CO₂ dovute ai gas fluorurati a effetto serra utilizzati negli impianti di climatizzazione e refrigerazione rappresenta uno strumento essenziale per raggiungere gli obiettivi di decarbonizzazione e quindi di lotta al cambiamento climatico. Lo scorso 16 gennaio i deputati del Parlamento europeo hanno approvato in seduta plenaria, con 457 voti favorevoli, 92 contrari e 32 astensioni, il testo proposto dalla Commissione per l’ambiente, la sanità pubblica e la sicurezza alimentare (ENVI) per la revisione del quadro legislativo sugli F-Gas che modifica la direttiva UE 2019/1937 e abroga il regolamento UE n. 517/2014.
Con questa decisione il Parlamento ha abbracciato una posizione molto ambiziosa, sostenendo il phase-down degli HFC sul mercato europeo e l’eliminazione completa di produzione e consumo entro il 2050, con una prima riduzione già a partire dal 2025. A tale scopo, il regolamento prevede il divieto di immissione sul mercato delle diverse tipologie di apparecchiature per impianti HVAC contenenti gas fluorurati secondo il programma temporale riportato nella tabella 1, ricavata da quanto indicato nell’Allegato IV del regolamento. La tabella indica anche i gas attualmente utilizzati per le diverse apparecchiature con il relativo GWP.
Per quanto riguarda le apparecchiature aventi una potenza nominale sopra i 50 kW, dal 2027 scatta il divieto per i chiller funzionanti con R410A e dal 2030 quello per le pompe di calore caricate con gas che hanno un GWP maggiore di 150, ovvero tutti quelli utilizzati attualmente. Gli impianti VRF funzionanti a 410A non potranno essere immessi sul mercato a partire dal 2029 mentre saranno ammessi fino al 2033 quelli caricati con R32.
L’uso dei gas nelle macchine e nei sistemi VRF esistenti sarà ovviamente consentito, così come la manutenzione delle apparecchiature già installate. Tuttavia, in caso di necessità di ricarica i costi potrebbero diventare sempre più elevati nei prossimi anni, dal momento che è prevista una progressiva riduzione delle tonnellate di CO₂ equivalente che potranno essere immesse sul mercato.
L’eliminazione graduale dei refrigeranti sintetici è solo uno degli aspetti affrontati dal regolamento F-Gas. Per ridurre la quantità di gas fluorurati che potrebbero disperdersi nell’atmosfera risulta necessario mettere in pratica anche le seguenti azioni:
- prevenire il rilascio di gas (intenzionale o non intenzionale);
- ridurre al minimo le perdite e garantire riparazioni tempestive quando rilevate;
- prevedere controlli regolari delle perdite e tenuta dei registri e, in alcuni casi, l’impiego di sistemi di rilevamento delle perdite;
- garantire il recupero dei gas per il riciclo, il recupero o lo smaltimento quando l’apparecchiatura viene smantellata o riparata;
- limitare la vendita di apparecchiature a imprese che non dispongono di adeguati titoli professionali;
- garantire la corretta etichettatura dei prodotti e delle apparecchiature.
In particolare il regolamento dedica due articoli ai controlli delle perdite e ai sistemi di rilevamento. L’articolo 5 prescrive che siano controllate per verificare la presenza di eventuali perdite le apparecchiature contenenti quantità pari o superiori a 5 tonnellate di CO₂ equivalente di gas elencati nell’allegato I oppure una quantità pari o superiore a 1 kg di gas elencati nell’allegato II, sezione 1.
Le apparecchiature ermeticamente sigillate, etichettate come tali, non sono soggette a controlli a condizione che contengano meno di 10 tonnellate di CO₂ equivalente di gas elencati nell’allegato I oppure meno di 2 chilogrammi di gas elencati nell’allegato II, sezione 1.
I controlli delle perdite devono essere effettuati con la frequenza seguente:
- almeno ogni 12 mesi per le apparecchiature contenenti meno di 50 tonnellate di CO₂ equivalente di gas elencati nell’allegato I oppure meno di 10 kg di gas elencati nell’allegato II, sezione 1. Se è installato un sistema di rilevamento delle perdite la frequenza è di almeno 24 mesi;
- almeno ogni 6 mesi per le apparecchiature contenenti tra 50 e 500 tonnellate di CO₂ equivalente di gas elencati nell’allegato I oppure tra 10 e 100 kg di gas elencati nell’allegato II, sezione 1. Se è installato un sistema di rilevamento, la frequenza è di almeno ogni 12 mesi;
- almeno ogni 3 mesi per le apparecchiature contenenti più di 500 tonnellate di CO₂ equivalente di gas elencati nell’allegato I oppure più di 100 kg di gas elencati nell’allegato II, sezione 1. Se è installato un sistema di rilevamento delle perdite, almeno ogni 6 mesi.
In pratica, l’impiego di un sistema di rilevamento consente quindi di dimezzare la frequenza dei controlli.
L’articolo 6 prescrive invece l’impiego di un sistema di rilevamento delle perdite che avverta l’operatore o l’impresa di manutenzione in caso di perdita per le apparecchiature fisse a servizio di impianti di refrigerazione e climatizzazione che contengono gas elencati nell’allegato I in quantità pari o superiori a 500 tonnellate di CO₂ equivalente oppure più di 100 kg di gas elencati nell’allegato II, sezione 1.
I sistemi di rilevamento delle perdite devono essere controllati almeno ogni dodici mesi per accertarne il corretto funzionamento. Come riferimento, si consideri che per l’R134, con GWP di 1430, 500 tonnellate di CO₂ equivalente corrispondono a una carica di 350 kg.
All’inizio del 2023 l’agenzia ha ricevuto una proposta di regolamentazione sviluppata da Germania, Paesi Bassi, Danimarca, Norvegia e Svezia, volta a limitare produzione, immissione sul mercato e uso delle PFAS, sostanze chimiche per-e polifluoro alchiliche, molto resistenti alla degradazione e che possono avere effetti negativi sulla salute e sull’ambiente. La proposta di regolamentazione riguarda direttamente il settore della climatizzazione poiché la maggior parte dei refrigeranti fluorurati, tra cui l’R134a e i suoi sostituti HFO, ad esempio R1234yf e R1234ze, ricade nella definizione di PFAS. Altri gas refrigeranti, come l’R32, non rientrano invece nella definizione di PFAS ma non è chiaro, nel caso in cui la proposta di regolamento dell’ECHA venisse adottata, se anch’essi finiranno o meno nella restrizione generale.
Ci troviamo quindi di fronte alla prospettiva che i gas fluorurati con un elevato potenziale di riscaldamento globale (dove per elevato si intende un GWP superiore a 1000) vengano gradualmente eliminati ai sensi del regolamento europeo sugli F-Gas, mentre per i loro sostituti, ovvero gli HFO con GWP molto basso, il divieto d’uso potrebbe avvenire in un arco di tempo più breve in base alla restrizione PFAS.
Ciò è dovuto al fatto che la ridotta vita atmosferica degli HFO, che conferisce loro un basso GWP, significa che vengono convertiti nei cosiddetti “inquinanti organici persistenti”, o POP (Persistent Organic Pollutants), molto più velocemente degli HFC, più stabili e quindi di più lunga durata, che dovrebbero sostituire. Nel caso in cui dovessero essere abbandonati HFC e HFO nello stesso lasso di tempo, dovrà essere migliorato in tempi ultrarapidi l’impiego in sicurezza dei refrigeranti infiammabili. Che si tratti di fluidi A2L come l’R32 oppure A3 come l’R290, sarà necessario un sostanziale ripensamento degli attuali standard. Ciò non significa che gli impianti diventeranno meno sicuri, a patto che il cambiamento venga gestito correttamente.
Requisiti di sicurezza per il rilevamento
I diversi standard di sicurezza si sono armonizzati a livello internazionale nei riguardi della progettazione, del funzionamento della manutenzione delle apparecchiature frigorifere installate nelle centrali tecniche degli edifici civili. Gli ASHRAE Standard 15 e 34 e la norma EN 378 rappresentano il riferimento per il settore, rispettivamente negli Stati Uniti e nell’Unione Europea, per quanto riguarda la sicurezza degli operatori e di qualsiasi persona possa avere potenzialmente accesso alle apparecchiature di una centrale tecnica in cui potrebbero essere presenti gas refrigeranti.
Questi standard definiscono l’uso corretto delle apparecchiature che contengono gas refrigeranti, la quantità massima della carica per specifici gas e i limiti di esposizione. La loro applicazione viene ulteriormente rafforzata dalle prescrizioni dei codici di prevenzione incendi a livello internazionale e locale, nonché dai regolamenti e dalle leggi nazionali o comunitarie, come il già citato regolamento F-Gas dell’Unione Europea e la legge EPA 608 negli USA.
A cominciare dagli anni 90, la maggior parte dei regolamenti relativi all’impiego delle apparecchiature frigorifere utilizzate negli edifici civili ha adottato questi standard per quanto riguarda l’uso sicuro degli impianti e dei gas refrigeranti. Questi standard sono rivolti alla prevenzione dei rischi e richiedono specificamente l’uso di rilevatori fissi nelle centrali tecniche.
Lo Standard ASHRAE 1 (al paragrafo 7.6.4) li richiede per apparecchiature con cariche superiori a 3 kg di refrigeranti di tipo CFC, HFC o HFO, mentre la norma EN 378 prevede limiti di carica superiori, ovvero 12 kg per l’R32, ma richiede che i rilevatori siano collegati al sistema di ventilazione di emergenza. La maggior parte degli edifici esistenti ad uso civile deve pertanto disporre di un sistema di rilevamento dei gas nelle centrali frigorifere in modo da proteggere la sicurezza del personale tecnico.
Sistemi di rilevamento a confronto
È importante comprendere la differenza tra lo scopo dei sistemi di rilevamento utilizzati per soddisfare gli standard di sicurezza rispetto a quello dei sistemi in grado di fornire un avviso tempestivo delle perdite, come previsto dal regolamento F-Gas.
La maggior parte dei rilevatori di sicurezza sono del tipo a diffusione. Essi sono comunemente montati a parete e richiedono che la perdita raggiunga l’elemento sensibile mentre la concentrazione si diluisce nel percorso dal punto della perdita fino alla posizione del rilevatore. Una volta rilevato il gas, l’allarme viene lanciato rapidamente. Se viene utilizzata una custodia con grado di protezione IP, i tempi di risposta potrebbero essere più lunghi.
I rilevatori a diffusione incorporano in genere un sensore di gas con un limite minimo rilevabile (MDL) di 100 ppm e con set point di allarme preimpostato dal 15 al 100% dell’intervallo di fondo scala. Il limite inferiore dell’intervallo riduce i falsi allarmi fornendo comunque un fattore di sicurezza di circa 7 volte prima di raggiungere la soglia del limite di esposizione professionale (OEL), che rappresenta l’intervallo del tipico set point superiore di allarme. Questo fattore di sicurezza diventa maggiore se si considera che l’OEL è tipicamente utilizzato come TLV-TWA (valore limite di soglia – media ponderata nel tempo) ed è definito come limite ponderato nel tempo di 8 ore.
Gli standard di sicurezza richiedono il rilevatore sia posizionato in una zona in cui si concentra il gas refrigerante derivante da una perdita. Il rilevatore deve attivare un allarme e la ventilazione meccanica in corrispondenza di un valore non superiore al TLV-TWA o di una misura simile di pericolo o di tossicità per il gas refrigerante. Lo scopo degli standard di sicurezza è quello di avvisare il tecnico responsabile del facility prima di entrare in un locale tecnico dove la concentrazione di gas potrebbe superare i livelli di concentrazione di sicurezza a causa di una perdita.
Altri valori limite degli standard di sicurezza, oltre all’OEL, sono il limite per esposizione di breve durata (STEL), con un TWA di 15 minuti, il pericolo immediato per la vita e la salute (IDLH), il limite di mancanza di ossigeno (ODL), il limite di esposizione alla tossicità acuta (ATEL) e il limite pratico. La tabella 2 mette a confronto i diversi valori limite previsti dalle norme ASHRAE e EN 378.
Esposizioni prolungate ai refrigeranti HFC o HFO possono causare effetti nocivi sulla salute dal punto di vista cardiologico e neurologico e possono, in concentrazioni più elevate, portare all’asfissia. È necessario considerare che il ppm (parti per milione) è un’unità di misura della concentrazione basata sul volume.
Sebbene questo tipo di rilevamento sia più che sufficiente per soddisfare la conformità in termini di sicurezza, in genere esso non risulta adeguato a individuare perdite di bassa entità, ridurre le emissioni di refrigerante dagli impianti e rispettare le normative e le leggi vigenti in materia. A tale scopo è necessario impiegare i sistemi di campionamento ad aspirazione che utilizzano un sensore di gas centralizzato molto sensibile con un MDL molto più basso, fino a 1 ppm, che consente di avere punti di allarme con concentrazioni da 5 a 10 ppm (figura 2).
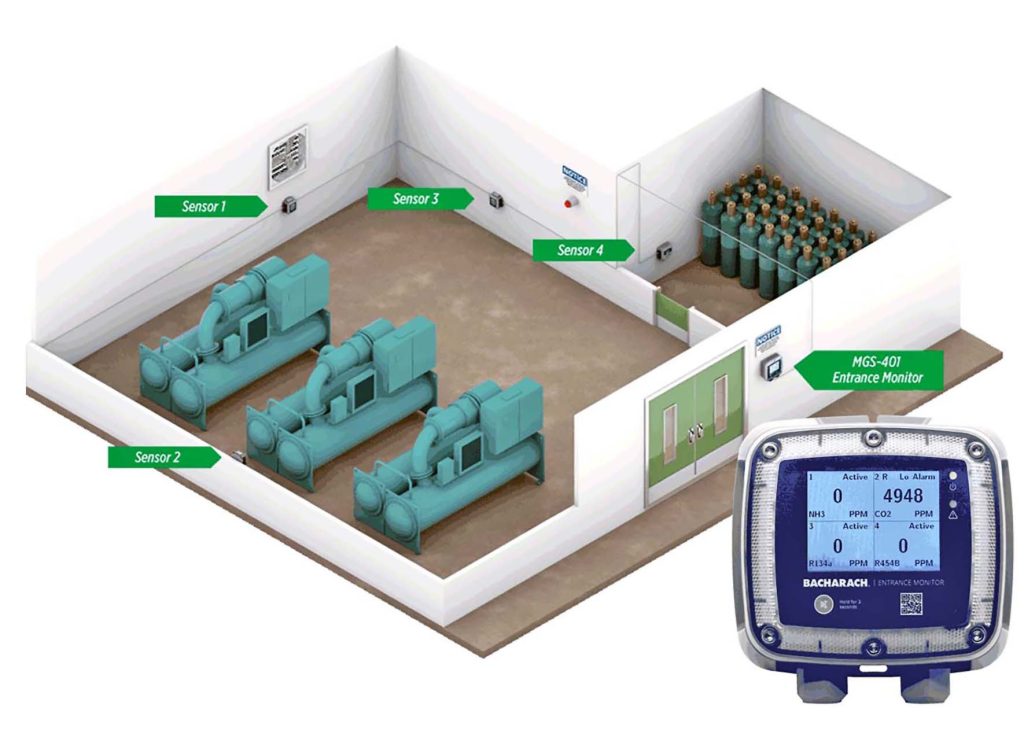
Inoltre, il posizionamento del punto di campionamento il più vicino possibile alla fonte della perdita migliora la capacità di rilevare precocemente perdite contenute.
Questi sistemi di campionamento sono ideali per applicazioni in edifici con molte potenziali fonti di perdite che possono diffondersi rapidamente in ampi spazi. Essere in grado di rilevare tempestivamente una fuga di refrigerante significa che questa può essere riparata il più rapidamente possibile e non rischia di trasformarsi in una perdita rilevante, di conseguenza è possibile ridurre al minimo i danni all’ambiente e avere tempi di inattività delle apparecchiature minimi o nulli.
Il costo delle apparecchiature per il rilevamento tempestivo delle perdite potrebbe sembrare una spesa elevata, soprattutto quando i budget sono limitati, tuttavia qualsiasi perdita di refrigerante rilevata e risolta il più presto possibile consente di ottenere un risparmio sui costi per la ricarica che può più che compensare il costo sostenuto. È anche importante considerare il fatto che nei prossimi anni i prezzi dei refrigeranti tenderanno ad aumentare in modo esponenziale.
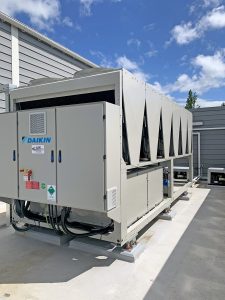
Soluzioni specifiche sono disponibili anche per il rilevamento delle perdite da gruppi frigoriferi ad aria installati all’esterno, per i quali non è ovviamente possibile misurare la concentrazione del gas disperso nell’ambiente. Un costruttore, ad esempio, ha sviluppato un software basato su un algoritmo che rileva i dati storici di funzionamento e che lancia un allarme in caso di fughe di gas anche di piccola entità. Il software è interfacciato con un sistema di monitoraggio da remoto su cloud.
Per la gestione dei sistemi VRF sono invece disponibili sistemi ad aspirazione con sensori e tubazioni per il campionamento, in grado di monitorare fino a 32 locali da un solo pannello. Il sistema effettua un autocontrollo continuo e rileva immediatamente qualsiasi perdita di refrigerante attivando un allarme e provvedendo al recupero automatico del refrigerante con ciclo di pump-down mediante sezionamento dei circuiti ottenuto con valvole a sfera motorizzate.
Allarme tempestivo per la riduzione delle perdite
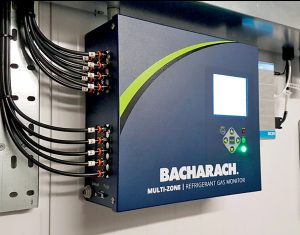
Le modalità di guasto più comuni che causano una perdita sono costituite dal pitting (vaiolatura), dalla corrosione o da piccole cricche da fatica dovute a ripetuti cicli termici. Le perdite di questo tipo sono inizialmente contenute, possono essere intermittenti e impiegare giorni o settimane per raggiungere livelli rilevabili nella zona di respirazione. Un sistema di rilevamento ultrasensibile a basso MDL (1 ppm) con punti di campionamento situati vicino alla fonte può fornire un allarme tempestivo e facilitare la riparazione ben prima che una cricca da fatica possa comportare concentrazioni dannose o semplicemente continuare nel tempo come una perdita lenta e costante di refrigerante nell’atmosfera. Il sistema viene gestito da un quadro locale di controllo che dispone di un ampio display grafico e di indicatori di stato a LED che forniscono una panoramica del funzionamento dell’intero sistema (figura 3).
Inoltre, sono disponibili numerosi protocolli di comunicazione, quali Modbus, BACnet e LonWorks, che consentono una facile integrazione nei sistemi BMS previsti per la supervisione. Inoltre, alcuni costruttori di questi sistemi possono fornire un servizio di monitoraggio da remoto connesso attraverso piattaforme che ricevono i segnali dai punti di campionamento.
La figura 4 rappresenta un tipico profilo di perdita in cui la concentrazione ha impiegato 28 giorni per superare il livello minimo di rilevamento tipico di un apparecchio a diffusione.
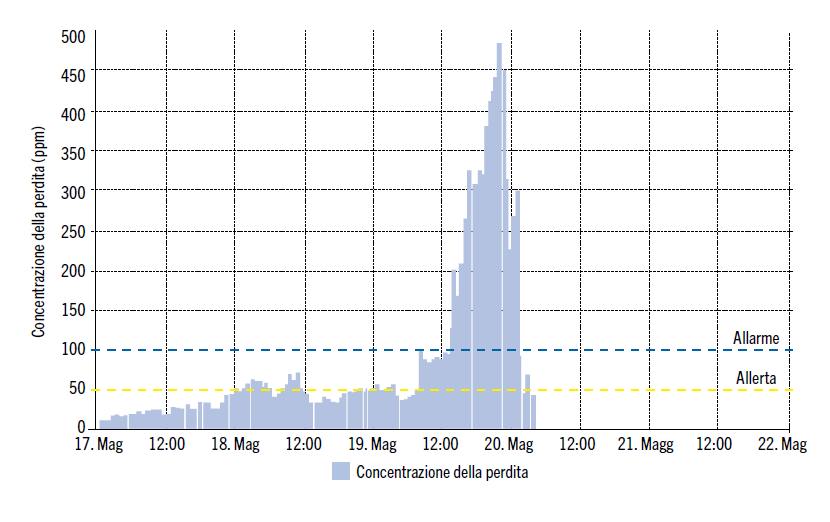
Si noti che questa concentrazione è stata rilevata vicino alla fonte della perdita, mentre quella vicino a un rilevatore di gas di sicurezza montato a parete sarebbe stata molto inferiore a causa della diffusione del gas e del movimento forzato dell’aria nel locale. Anche se questa perdita raggiungesse l’MDL di un rilevatore di gas a diffusione, bisogna considerare che i tipici punti di allarme dei rilevatori di gas a diffusione sono dell’ordine di centinaia di ppm.
Il diagramma di figura 5 mostra i risultati di una ricerca condotta dall’Unione Europea per ridurre le emissioni identificando e documentando le comuni perdite di refrigerante. La ricerca ha rilevato che dei 1036 punti dati monitorati, circa l’82,4% aveva dimensioni inferiori a 0,05 mm2 e il 94,9% aveva dimensioni inferiori a 0,10 m2.
Inoltre, è stato dimostrato che le fonti delle perdite sono dovute a linee frigorifere incrinate o affaticate, a corrosione sulle batterie dell’evaporatore e del condensatore e a perdite di valvole e guarnizioni. Ciò conferma ulteriormente i risultati dello studio condotto dall’EPA negli Stati Uniti. Le dimensioni di una centrale termofrigorifera possono variare a seconda delle dimensioni dell’edificio e del carico frigorifero e in molti casi la centrale può ospitare uno o più chiller o pompe di calore.
La figura 6 mostra una centrale con un volume di 300 m3 con tre gruppi frigoriferi che contengono decine di kg ciascuno di refrigerante. Una tipica centrale potrebbe avere una ventilazione da 5 a 10 ricambi orari, anche se una buona prassi ingegneristica è di avere fino a 15 ricambi.
Per confermare ulteriormente quanto sia difficile per una piccola perdita raggiungere le concentrazioni di allarme è possibile calcolare la concentrazione nella centrale allo stato stazionario per un dato tasso di perdita e di ricambio e le caratteristiche dimensionali sopra descritte e utilizzando la seguente equazione:
Concentrazione di gas = tasso di perdita/(ricambio orario x volume dell’ambiente).
La tabella 3 e la figura 7 mostrano come la concentrazione allo stato stazionario dell’R410A raggiunga il valore di 4,6 ppm con 5 ricambi orari. Questo valore non raggiunge il livello minimo di rilevamento di un apparecchio a diffusione (100 ppm). Inoltre, se si adottasse la buona prassi di prevedere una ventilazione forzata compresa tra 10 e 15 ricambi, si avrebbe un’ulteriore diluizione della concentrazione di gas. L’ampio spazio e la ventilazione forzata del locale tecnico dirigono e diluiscono le perdite di gas impedendo alla maggior parte di queste apparecchiature di fornire un reale rilevamento sotto forma di segnali di preallarme che garantiscono una maggiore sicurezza e una riduzione delle emissioni.
Va inoltre considerato che, anche se l’aria nel locale tecnico non presenta pericoli per il personale secondo gli standard di sicurezza, il tasso di perdita e la quantità della carica assunti nei calcoli determinano una perdita di circa 160 kg di refrigerante ogni anno.
Questo scenario potrebbe comportare in 10 anni di vita utile della macchina una perdita totale di 1600 kg di refrigerante, dato che la bassa concentrazione non attiva l’allarme da parte di un rilevatore di gas a diffusione. Pertanto, in base alla dimensione e alla quantità delle perdite e alla loro tendenza a diffondersi a causa della ventilazione forzata o ad accumularsi a causa delle differenze di densità, i rilevatori di gas di sicurezza non forniscono un allarme tempestivo in caso di perdite contenute.
Al contrario, è stato dimostrato che i sistemi di rilevamento multipunto ultrasensibili ad aspirazione forniscono un allarme immediato anche in caso di perdite minime e quindi consentono di ridurre le emissioni di refrigerante e di aumentare la sicurezza.
Sono molti gli aspetti che differenziano i sistemi di rilevamento ad aspirazione rispetto a quelli a diffusione. I tre aspetti più importanti sono i seguenti:
- il set point di allarme minimo consentito dello strumento di rilevamento del gas;
- la vicinanza dei punti di rilevamento rispetto ai punti di perdita dei componenti dell’impianto frigorifero e alla ventilazione forzata,
- il numero dei punti di rilevamento utilizzati nella centrale.
Le soglie minime d’allarme
Come accennato in precedenza, i rilevatori di gas di sicurezza prescritti dalle norme ASHRAE 15 e EN 378 sono generalmente preimpostati con soglie di allarme comprese tra il 15 e il 100% del fondo scala e sebbene ciò sia sufficiente per proteggere il personale dall’esposizione a concentrazioni pericolose e nocive, è improbabile che un set point di allarme compreso tra 100 e 1000 ppm sia in grado di avvisare in caso di minime perdite di gas.
Il set point di allarme minimo di un rilevatore di gas è determinato dal livello di rilevamento minimo (MDL), che è una misura della sensibilità della tecnologia del sensore di gas del rilevatore. L’MDL non deve essere confuso con l’intervallo o la precisione di rilevamento. Rappresenta la concentrazione più bassa (ovvero 100, 10 o 1 ppm) che il rilevatore può rilevare del gas di target (ad esempio R410A).
Poiché le perdite di gas refrigerante possono essere piccole e diluite negli spazi ampi delle centrali tecniche, i rilevatori fissi con MDL molto più bassi possono abilitare setpoint di allarme a livelli inferiori a 5-10 ppm. La possibilità di attivare un allarme a questa soglia aumenta notevolmente la probabilità di rilevare una perdita di modesta entità.
Sebbene il produttore di uno strumento di rilevamento possa o meno specificare l’MDL, dovrebbe specificare il set point di allarme minimo consentito, che non dovrebbe essere inferiore all’MDL. I set point di allarme impostati al di sotto dell’MDL del rilevatore di gas possono causare ripetuti falsi allarmi o potrebbero non emettere alcun allarme.
Prossimità dei punti di rilevamento
Il progressivo invecchiamento dei gruppi frigoriferi nel corso degli anni aumenta ovviamente il rischio di perdite. Le guarnizioni dei compressori e delle valvole possono usurarsi o rompersi e non riuscire a garantire la tenuta. Sulle tubazioni possono anche formarsi crepe a causa dei ripetuti cicli termici o per corrosione per vaiolatura e quindi possono iniziare a verificarsi una perdita.
Sebbene all’inizio questa può essere piuttosto piccola e intermittente, la sua velocità tende ad aumentare nel tempo. La densità della maggior parte dei gas refrigeranti è più pesante o più leggera della densità dell’aria circostante e pertanto si corre il rischio che essi cadano verso il pavimento oppure salgano verso il soffitto formando sacche di gas che possono aumentare di concentrazione. Le piccole perdite e le sacche di concentrazione possono essere spazzate via dalla ventilazione ad aria forzata. Ne consegue che la collocazione ideale del punto di rilevamento deve essere il più vicino possibile ai comuni punti di perdita dell’apparecchiatura e possibilmente a valle della direzione del flusso della ventilazione del locale.
Alcuni produttori di rilevatori di gas di sicurezza suggeriscono un raggio di 7-9 metri per determinare la posizione e il numero di rilevatori in un dato spazio. Il concetto di “raggio di rilevamento” è un approccio semplicistico e rende molto meno probabile che il rilevatore si trovi vicino a una fonte di perdita, riducendo così la probabilità di rilevarne una di basso livello. Questo metodo di rilevamento del gas è ulteriormente compromesso dai flussi d’aria forzata in una tipica centrale.
Numero di punti di rilevamento
Come visto in precedenza, le norme ASHRAE 15 e EN 378 attualmente richiedono almeno un punto di rilevamento del gas all’interno di un locale tecnico. La figura 9 mostra un esempio di una centrale dotata di un sistema di rilevamento di sicurezza a diffusione con sensore di gas montato sulla parete a un’altezza di 450 mm da terra e di un lampeggiante e avvisatore acustico posto all’esterno della porta di ingresso al locale che avvisa se la concentrazione supera il punto di allarme impostato.
L’impiego di un singolo punto di rilevamento risulta generalmente sufficiente per determinare se l’aria del locale è sicura. Per ottenere un efficace e immediato rilevamento delle perdite, tuttavia, il numero di punti di rilevamento dovrebbe essere associato al numero dei comuni punti di perdita dei gruppi frigoriferi.
La figura 10 mostra un esempio di centrale dotata di un sistema di rilevamento ultra sensibile ad aspirazione, che fornisce il numero più conveniente di punti di campionamento con il valore di MDL più basso possibile. Il sistema multipunto prevede un sensore di gas ultrasensibile posizionato centralmente e una pompa di aspirazione per prelevare campioni in più posizioni significative della centrale.
I punti di rilevamento sono semplici terminali di tubi pneumatici senza la necessità di alimentazione elettrica e possono essere montati facilmente e in sicurezza sopra o vicino alla fonte della perdita. Nella figura 10 i punti di campionamento pneumatico di un monitor di gas ultrasensibile sono posizionati in prossimità di tipici punti di perdita quali linea di aspirazione, valvola di espansione, guarnizione del compressore e linee di alimentazione del refrigerante.
Le zone di monitoraggio della concentrazione di gas possono essere ampliate utilizzando dispositivi che aumentano la copertura. Questa espansione può essere realizzata con un monitor del refrigerante a zona singola oppure multizona in grado di aumentare ciascuna delle zone disponibili di 2-3 volte.
La tabella 4 riassume e mette a confronto le prestazioni dei due sistemi di rilevamento in funzione dell’entità delle perdite e della probabilità che si verifichino. Generalmente le perdite di entità ridotta sono quelle che presentano la maggiore probabilità, al contrario di quelle elevate che sono meno frequenti.
Dalla tabella risulta chiaro che i sistemi ad aspirazione risultano efficaci in ogni situazione mentre quelli a diffusione lo sono soltanto in presenza di perdite consistenti, prevendo in ogni caso una calibrazione annuale del punto di rilevamento e un’ispezione visiva di routine per verificare il percorso di diffusione del gas.
In caso di perdite di media entità l’efficacia dei sistemi a diffusione dipende dal flusso d’aria forzata e dal posizionamento del sensore nella centrale tecnica.
Conclusioni
La legislazione sui gas fluorurati, con le sue fasi di riduzione graduale di impiego, ha l’obiettivo di ridurre le emissioni di tonnellate equivalenti di CO₂ e quindi di minimizzare le perdite di refrigerante adottando tutte le misure necessarie. La regolamentazione ha già prodotto negli ultimi anni un notevole progresso in termini di migliore tenuta dei circuiti frigoriferi, operazioni di manutenzione più accurate, formazione e qualificazione dei tecnici frigoristi, adozione diffusa di procedure di recupero e riciclo del refrigerante e utilizzo di gas con GWP inferiori.
I rilevatori di gas progettati per garantire la sicurezza in conformità alla norma EN 378 e agli standard ASHRAE 15 e 34 sono senza dubbio utili per proteggere il personale che deve entrare in una centrale tecnica con concentrazioni di refrigerante che potrebbero essere dannose per la salute. La tipologia, l’ubicazione e il numero di sensori previsti dagli standard di sicurezza non sono tuttavia generalmente sufficienti a individuare le perdite più comuni e più piccole che nel corso del tempo spesso si trasformano in rilevanti emissioni di gas refrigerante, con una progressiva riduzione dell’efficienza dei gruppi frigoriferi e dei livelli di sicurezza per gli operatori.
È quindi necessario fare un salto di qualità per rispondere agli effetti della regolamentazione che impone l’eliminazione graduale dei refrigeranti sintetici. Sotto questo aspetto l’utilizzo di sistemi ad aspirazione in grado di garantire un rilevamento tempestivo di perdite anche di piccola entità riveste un ruolo importante per mantenere l’efficienza ottimale dell’impianto, riducendo consumo di energia e la quantità di refrigerante disperso nell’ambiente.